Jet Milling To Break The Rock
2020-03-01T23:03:53+00:00

Study on the rock‐breaking effect of water jets generated by
2020年3月11日 For the appearance of a deeper and wider crater, the optimized standoff distance was ranged from 20 to 30 mm Similar experiment conducted by Ren et al 11 Contribute to hongyib/fr development by creating an account on GitHubfr/jet milling to break the rockmd at main hongyib/fr2021年7月18日 Its sandstonebreaking characteristics are researched by experiment, the influence of working conditions, lithology, axis length, jet pressure (15 ~ 40 MPa), and Rock Breaking Characteristics of the Selfrotating Multi2023年8月15日 With the continuous development of highpressure water jet technology, research on the optimization of structural parameters for multinozzle configurations, the Sustainability Free FullText Analysis of Rock Breaking 2020年9月1日 Mathematical simulations for breakage rate and breakage function of jet mill [33] Comminution principle: Compression, impact, abrasion and attrition – – Breakage process of mineral processing comminution

Numerical research on the dynamic rockbreaking process of
2021年12月1日 Through a large number of studies and experiments on the rock breaking mechanism, the basic process of rock breaking, and the theoretical model of rock 2020年5月21日 The results show that there exists an optimal standoff distance for the single water jet under the condition of maximum removal volume, that is 15 mm in this Study of the rockbreaking and drilling performance of a self 2022年11月1日 The swirling impeller nozzle is expected to drill large diameter radial branches in HDR However, the swirling impeller water jet (SWJ) is difficult to break hard Rock breaking characteristics by swirling impeller abrasive water jet On this basis, considering the correlation between free surface and milling, the mechanism of the influence of cutting sequence on rock breaking performance of tooth arrangement system is studied Rock break mechanisms: (a) single joint coupled 2020年7月2日 nozzle17,18 It is found that the rockbreaking effect of water jets produced by multiorifice nozzle increases linearly with the jet pressure, and there exist maximum Study on the rock‐breaking effect of water jets
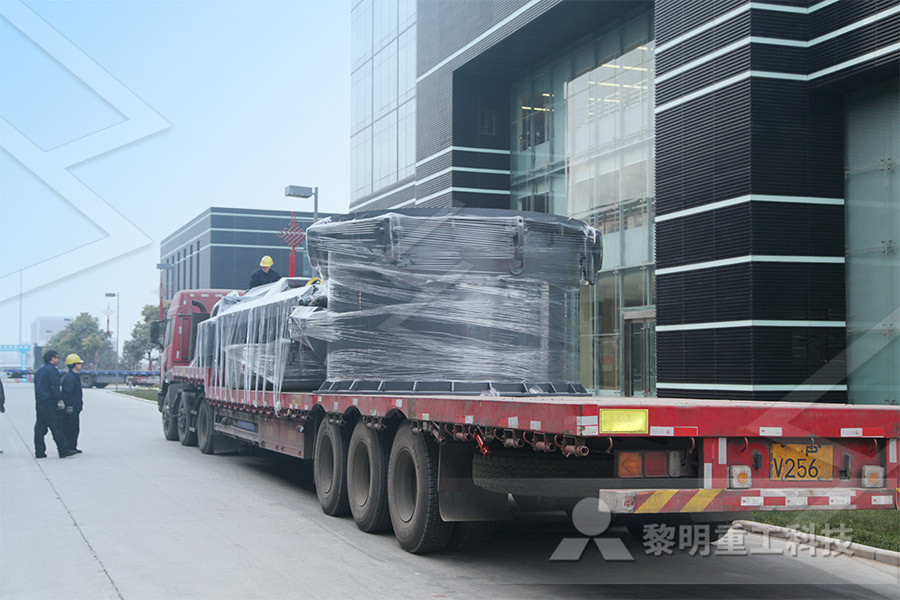
Experiment on micronsized particle production of iron ore
2018年3月1日 Section snippets Introduction of rapid unloading of liquid CO 2 used in the production of micronsized iron ore particles The rapid unloading of liquid CO 2 is as follows: the whole process is carried out in a highpressure chamber, which consists of a rupture disk, seal cover and sealing ring, inlet control valve and needle valve The 2017年10月23日 ness ranging from 1 to 5, while a jet mill can grind materials with Mohs hardness as high as 10 High hardness materials become very abrasive; therefore, they are not suitable for highspeed hammer mills In a typical jet mill, grinding action is caused mainly by particleparticle collisions, so wear to the mill’s internals is less of an issueBack to Basics Hammer Milling and Jet Milling Zhang et al [18] have designed and developed TBM coupled with highpressure water jet and mechanical cutter to create a free surface on intact rock samples by means of prefabricated kerf and Rock break mechanisms: (a) single joint coupled 2019年9月6日 Operating conditions to run the 4” jet mill are determined using statistical analysis The optimum operating conditions to run the jet mill are measured and the optimization procedure of the grinding process for ultrafine metallurgical powders in a smallscale 4” jet mill is derivedProcess optimization of jet mills for metallurgical Download scientific diagram Disc cutter positions during rock breaking tests with: (a) single or (b) double kerfs from publication: Using a highpressure water jetassisted tunnel boring Disc cutter positions during rock breaking tests with: (a)

Experimental study on rockbreaking performance of
2019年3月15日 And rockbreaking volume can be considered as the comprehensive evaluation index of water jet rockbreaking performance to a certain extent [38, 39] Besides, the specific energy consumption, which refers to the energy consumption of rock fragmentation per unit volume, is a key index to estimate the performance of rock 2017年8月25日 the nozzle of a pneumatic jet mill is low and is close to pneumatic transport velocities Figure 2a presents the plots of the particle acceleration efficiency versus η at two values of the relative gas velocity at the inlet of the nozzles of an ejector (λ in = 1) and a pneumatic (λ in = 02) jet mill A comparison between the plots showed thatModeling and Optimization of Jet Milling Springer2018年10月31日 Mechanical specific energy (MSE) has been widely used to quantify drilling efficiency and maximize rate of penetration (ROP) in oil and gas wells drilling In this chapter, MSE models respectively for directional or horizontal drilling and rotating drilling with positive displacement motor (PDM) are established based on the evaluation of Drilling Performance Optimization Based on Mechanical Specific Energy 2022年10月1日 The performance of WJD has been tested experimentally on different types of rock and the corresponding failure mechanisms have been analysed 4, 6, 8, 11, 12, 13 Dehkhoda and Hood, 11 who examined pulsed jet damage to granite and marble, based their interpretations of crack development on impact cratering phenomena 14 in Fig 1 a Numerical simulation of rock erosion performance of a high What is Cryogenic Milling? Cryogenic milling, or cryomilling, is the process of using liquid nitrogen to lower the temperate of the material and/or the milling process AVEKA ‘s cryogenic hammer mills can typically reduce the particle size from small pellets down to the 100s of microns Cryomilling can be used for:Cryo Milling Material Milling AVEKA

刨(planing)、铣(milling)、磨(grinding)等加工一金属平面
2014年8月5日 这个其实这样的,刨一般用于 加工余量 多的粗加工,工件表面的 粗糙度 高,效率最高;铣(可以单不限于表面)工艺加工表面,算是半 精加工 ,可以去除大的工件余量,效率也很高,工具主要是 面铣刀 ,进度能控制在002,技术好的话;磨,则是完全精加 2023年3月23日 The jet stream generates extreme forces that break up particles into smaller sizes, resulting in fine powders with uniform particle size distribution The heart of the jet milling process is the Understanding the Working Principle of Jet Mill 2009年7月1日 The optimum feed rate, classifier rotational speed, and grinding pressure for talc were 12 kg/h, 7000 rpm, and 6 bar, respectively Ground talc exhibited mechanochemical effect where the degree of crystallinity ranged from 265% to 853% Talc ground at 4 kg/h, 13,000 rpm, and 6 bar exhibited massive mechanochemical effect Mechanochemical effects on talc during fine grinding process in a jet mill2012年11月1日 气流粉碎机(Jet Mill)调研报告ppt 上传 气流粉碎机(Jet Mill)调研报告 精心收集的各类精品文档,欢迎下载! 文档格式:ppt 文档大小: 5885K 文档页数: 13 页 顶 /踩数: 0 / 0 收藏人数 气流粉碎机(Jet Mill)调研报告 豆丁网2017年1月17日 Excessive mill speeds caused more power consumption but resulted in reduced grinding rate Based on the simulation data, two scaleup models were proposed to predict power draw and grinding rate(PDF) Breaking down energy consumption in industrial
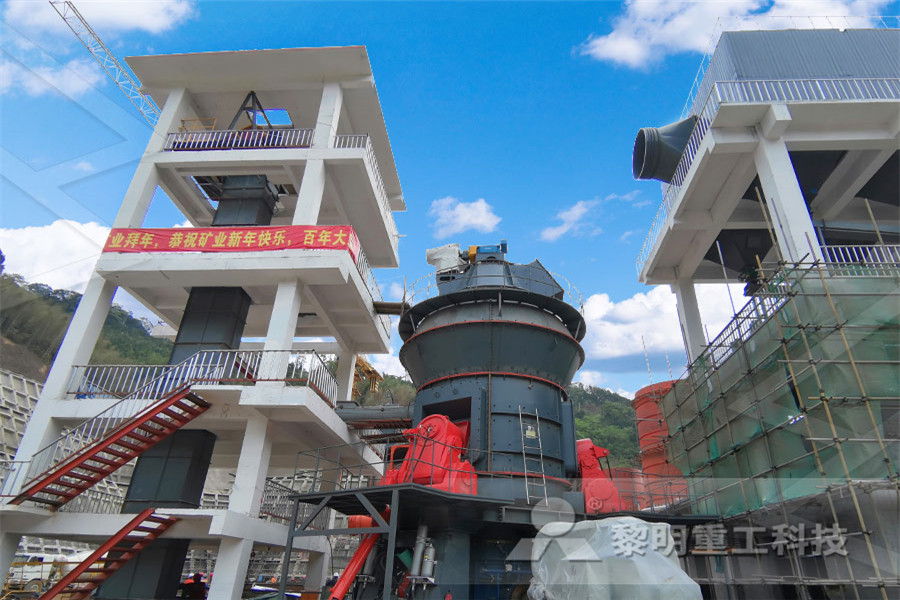
Analysis of grinding in a spiral jet mill Part 1: Batch grinding
2021年2月15日 The air jet mill is suitable for grinding materials with a wide range of hardness and the effect of hardness and energy input is related to the size of fragments by a simple scaling (Vogel and Peukert, 2003, Lecoq et al, 2011) The efficiency of grinding has been considered primarily in terms of the specific energy consumption Midoux et al 2021年4月16日 The paper describes the comminution process that takes place in the jet mill using a modified form of the thermodynamic theory of grinding In this theory, new material characteristics have been (PDF) Research on the Grinding Energy Density in a Jet Mill2019年6月1日 Strontium hexaferrite (SrFe 12 O 19) powders synthesized via conventional solidstate route are mechanically milled using air jetmill and ballmill techniques to produce anisotropic SrFe 12 O 19 powders Jetmilled and dry ballmilled powders showed higher strain (013%) compared to wet ballmilled powders (005%) On annealing, jetmilled Effect of jet milling on the physicochemical properties, 2023年8月3日 The mechanical action used to break the particles and reduce the size can be diverse and different mill exist that will use the milling principles Typical milling principles are the following : Use of 2 solid surfaces : the solid is pressed or frictionated against 2 solid surfaces Use of a single solid surface : the solid is impacted against Solids and powder milling Size reduction PowderProcess2019年10月1日 In general, smaller particles are more difficult to break than larger ones, since smaller particles contain fewer flaws and require more impact events to affect their fracture [20,21] The process flow for the QYF−260 fluidized bed jet mill is shown in Fig 1 The jet mill is mainly composed of an air compressor, a gas tank, a freeze Effect of jet milling on microstrain behavior and rupture behavior

A new solution to enhance cuttings transport in mining
2018年8月10日 This paper presented a new solution to enhance cuttings transport in mining drilling through a new type of bit called pulsed mill bit (PMB) by using pulse jet mill technique It provides a promising solution to enhance the efficiencies of rock breaking and cuttings carrying for pulsed jet, sucking cuttings to decrease the chip hold down effect 2020年2月20日 Mechanical crushing, ball milling, pin milling and jet milling are currently common methods for reducing the particle size of materials Experiments have shown that all of the above methods can break carbonized TiBFS to below 150 μmParticle size controllable jet milling technology for efficiently 2023年1月24日 Jet milling tray systems are designed to provide an RD jetmilling system that can efficiently mill and collect your fine powders in three batch ranges all in one system Each system is capable of maintaining yields in excess of 95% Different collection vessels designed for various batch sizes are easily attached to the portable mill by quick Jet Mills Glen Mills, Inc2019年9月6日 Operating conditions to run the 4” jet mill are determined using statistical analysis The optimum operating conditions to run the jet mill are measured and the optimization procedure of the grinding process for ultrafine metallurgical powders in a smallscale 4” jet mill is derivedProcess optimization of jet mills for metallurgical 2021年11月1日 The rockbreaking area and volume of the selfrotatory bit water jet were analyzed, and the effects of the nozzle distribution radii, jet pressure and rock strength on the rockbreaking and hole Rock Breaking Characteristics of the Selfrotating Multi

Water jet milling experiments on Brazilian stone
2004年1月1日 Download Citation Water jet milling experiments on Brazilian stone Abrasive Water Jet used to mill dimension stone tiles is a process known as rock milling This process is the most advanced 2004年11月1日 It mainly concerns optimisation of the operating and construction parameters such as; air flow rate, rotor speed, nozzle distance and mill filling level (Kolacz, 1999) The paper describes an optimisation process carried out in industrial conditions using many jet mill units producing different material under various conditionsProcess efficiency aspects for jet mill plant operation2019年7月31日 wetjet milling process and (b) the CNT dispersion with using wetjetmilling process sample, which applied the wetjet milling process, did not show sedimentation of CNT for more than a month, even if the processing times number was is result indicates that the wetjet milling process allows dispersing the CNT into waterResearch Article Fabrication of CNT Dispersion Fluid by 2022年6月21日 Video credit: shsbjq / CC BYSA 40 Specifications Important specifications when selecting grinding mills and pulverizers include, The size of the mill can range from pilot/lab to production, eg, 35 to 1600 cu ft; Feed size, material, and hardness of feed must be considered; Output size ranges; Mills can handle dry or wet input, or Grinding Mills and Pulverizers Selection Guide: Types, 2017年8月25日 sion are the main disadvantages of jet mills as compared to, eg, hammer, ball, and vibratory mills In conventional ejector jet mills, the mixing of the gas and particles takes place in a highvelocity turbulent jet (Fig 1a) and is characterized by significantly nonequilibrium phase velocities and, hence, a high energy lossModeling and Optimization of Jet Milling Springer
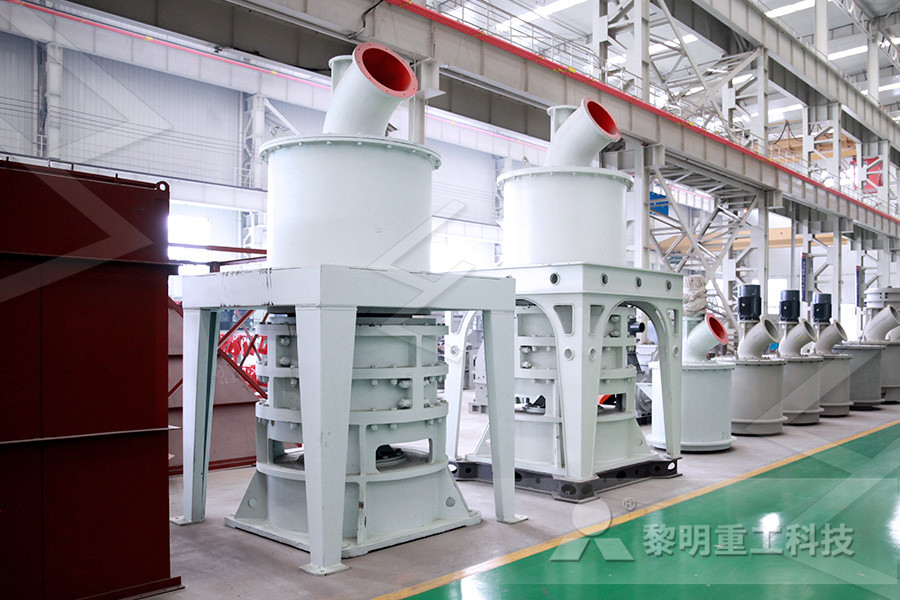
JET MILLING METHOD European Patent Office EP
2020年3月28日 micronizing source powders is jet milling [0003] The multiple high speed/high energy collisions that occur within the grinding chamber of a jet mill provide the milling action which is required to break the particles down to the appropriate size This process, however, can result in2018年10月1日 气流粉碎 1 Research on superfine jet mill s dynamic parameter by the orthogonal experiment; 超微 气流粉碎 机动态参数的正交试验研究 2 As an effective powder pulverizing technique, jet mill has been widely used in chemical industry,pharmaceutics and aviation 气流粉碎 技术是一种有效的粉末细化方法,目前 气流粉碎,jet milling,音标,读音,翻译,英文例句,英语词典2020年10月16日 5 Conclusions (1) The experiment results show that the rockbreaking performance of the pulsed water jet is much better than that of the continuous water jet While the fluid entrance is open and the external water is drawn in, the rockbreaking performance of the pulsed water jet will be improved significantlyExperimental Study on the Dynamic RockBreaking The Monteggio site is an integral component of our drug product design, development and manufacturing services network With 19 production suites and 37 cGMP jet and pin mills, the site is well equipped to support your compound at any point of the product lifecycle We provide micronization services from a few grams to tons of APIsJet Milling and Micronization Services Particle Engineering2020年9月22日 size Impact velocities in a fluid bed jet mill can range from 300500 meters per second, compared to 50150 meters per second in a mechanical impact mill A fluid bed jet mill’s highenergy micronization lower chamber can be combined with an integral forced vortex air classifier, allowing for greater control of the maximum particle sizeMILLING METHODS COMPARISON GUIDE Custom

Rock breaking characteristics by swirling impeller abrasive water jet
2022年11月1日 Thus, SAWJ is expected to break hard rock effectively and create a large hole The usage of the SAWJ is mostly windowmilling on the casing The experimental results of Zhou showed that the SAWJ could create a circular hole of 35 mm diameter on a 15 mm casing 50 Yang 51 investigated the rockbreaking performance on sandstone via Particle size reduction is a key process in laboratories and small scale manufacturing, right through to full size production Dec can integrate various milling equipment into their process solutions including Dec's crusher, CoMill, hammer mill, UMS and Dec's jet mill range In order to reduce particles of a few millimeters to less than 10 PST Particle Size Technologies Dec Group2019年10月31日 The rotation and revolution nanopulverizer is a batchtype wet pulverizer that can perform pulverization and disintegration into about 1 mm or less or even about 100 nm (several dozens of nm by disintegration) It is a type of planetary ball mill (planetary mill) or bead mill Introduce balls (also called beads), which are grinding media, into Pulverization 2: Pulverization method and pulverizer2017年10月23日 ness ranging from 1 to 5, while a jet mill can grind materials with Mohs hardness as high as 10 High hardness materials become very abrasive; therefore, they are not suitable for highspeed hammer mills In a typical jet mill, grinding action is caused mainly by particleparticle collisions, so wear to the mill’s internals is less of an issueBack to Basics Hammer Milling and Jet Milling Zhang et al [18] have designed and developed TBM coupled with highpressure water jet and mechanical cutter to create a free surface on intact rock samples by means of prefabricated kerf and Rock break mechanisms: (a) single joint coupled

Process optimization of jet mills for metallurgical
2019年9月6日 Operating conditions to run the 4” jet mill are determined using statistical analysis The optimum operating conditions to run the jet mill are measured and the optimization procedure of the grinding process for ultrafine metallurgical powders in a smallscale 4” jet mill is derivedDownload scientific diagram Disc cutter positions during rock breaking tests with: (a) single or (b) double kerfs from publication: Using a highpressure water jetassisted tunnel boring Disc cutter positions during rock breaking tests with: (a) 2019年3月15日 And rockbreaking volume can be considered as the comprehensive evaluation index of water jet rockbreaking performance to a certain extent [38, 39] Besides, the specific energy consumption, which refers to the energy consumption of rock fragmentation per unit volume, is a key index to estimate the performance of rock Experimental study on rockbreaking performance of2017年8月25日 the nozzle of a pneumatic jet mill is low and is close to pneumatic transport velocities Figure 2a presents the plots of the particle acceleration efficiency versus η at two values of the relative gas velocity at the inlet of the nozzles of an ejector (λ in = 1) and a pneumatic (λ in = 02) jet mill A comparison between the plots showed thatModeling and Optimization of Jet Milling Springer2018年10月31日 Mechanical specific energy (MSE) has been widely used to quantify drilling efficiency and maximize rate of penetration (ROP) in oil and gas wells drilling In this chapter, MSE models respectively for directional or horizontal drilling and rotating drilling with positive displacement motor (PDM) are established based on the evaluation of Drilling Performance Optimization Based on Mechanical Specific Energy

Numerical simulation of rock erosion performance of a high
2022年10月1日 The performance of WJD has been tested experimentally on different types of rock and the corresponding failure mechanisms have been analysed 4, 6, 8, 11, 12, 13 Dehkhoda and Hood, 11 who examined pulsed jet damage to granite and marble, based their interpretations of crack development on impact cratering phenomena 14 in Fig 1 a What is Cryogenic Milling? Cryogenic milling, or cryomilling, is the process of using liquid nitrogen to lower the temperate of the material and/or the milling process AVEKA ‘s cryogenic hammer mills can typically reduce the particle size from small pellets down to the 100s of microns Cryomilling can be used for:Cryo Milling Material Milling AVEKA