Ball Mill Media Charge Pattern
2021-10-05T15:10:58+00:00
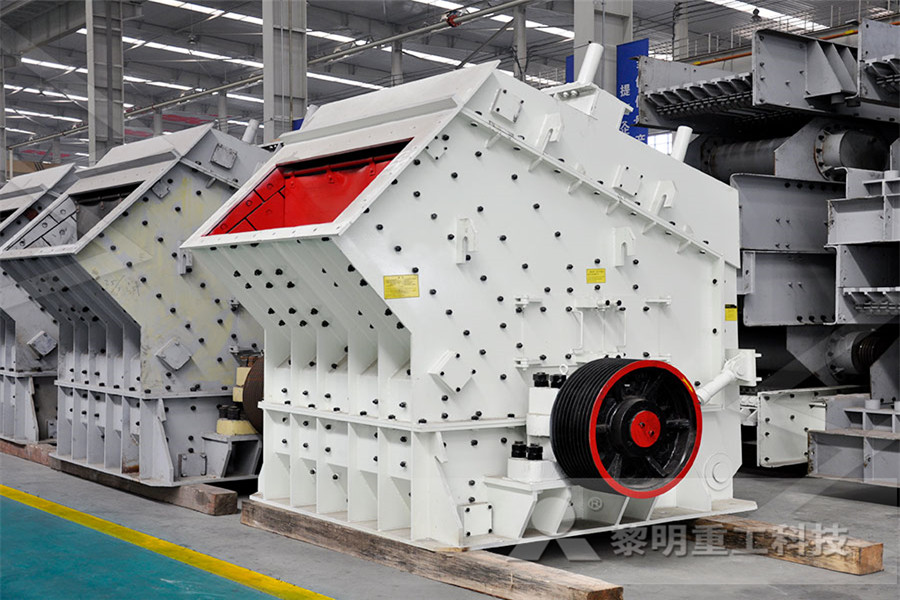
Understanding fine ore breakage in a laboratory scale ball mill using
2011年2月1日 Many researchers have used DEM to estimate media motion in ball mills, but the huge numbers of ore particles have often precluded their inclusion in these 2001年8月1日 Add to Mendeley https://doi/101016/S03017516 (01)000370 Get rights and content Discrete element method (DEM) modelling has been used to systematically Charge behaviour and power consumption in ball mills: 2018年12月4日 Ball mill media optimization through functional performance modeling by W Conger, JF DuPont, RE McIvor, TP Weldum The objective of the Figure study Ball mill media optimization Metcom TechThe starting point for ball mill media and solids charging generally starts as follows: 50% media charge; Assuming 26% void space between spherical balls (nonspherical, irregularly shaped and mixedsize media will Ball Mill Loading Dry Milling Paul O Abbe2018年6月1日 Mixture of different sized grinding media • Optimization of a desired product size class In this article, alternative forms of optimizing the milling efficiency of a Effect of ball and feed particle size distribution on the milling

DESIGN OF AN AUTOMATED GRINDING MEDIA
2023年6月26日 The principal aim in optimisation of grinding media charging is to reduce the costs of procuring the grinding media, replacing liners inside the ball mill and Reading Lecture In ball mills, steel balls or hard pebbles to break particle based on impact and attrition A rotating mill charged with media and ore is lifted against the inside perimeter Some of the media falls and impacts AMIT 135: Lesson 7 Ball Mills Circuits – Mining 2013年8月1日 The mill charge consisted of a set of 200 balls including 25 marked ones After each grinding experiment the 25 marked balls were washed, dried and weighed Consumption of steel grinding media in mills – A review1995年1月1日 This study emphasizes and the testing of alumina particles via a fabricated planetary ball mill The fabrication of planetary ball mill work began with the design of the (PDF) Ball Charge Dynamics in a Planetary Mill ResearchGateStirred Mills – Ultrafine Grinding In Mineral Processing Design and Operations (Second Edition), 2016 1024 Operation of Vertical Mills Vertical stirred mills are usually charged with media occupying 80% of the mill volume which is in sharp contrast to tumbling mills that are seldom charged more than 40% of their volumes to allow space for the tumbling Stirred Mill an overview ScienceDirect Topics

Day 1 5 BALL Mill Internals MBu PDF PDF
2018年10月15日 Ball Charge Management Deciding the Pattern Second Chamber – If the first chamber of the mill is achieving 2,5% residue on 1mm then there is no requirement for large media in the second chamber of a 2021年7月27日 Figure 511 Power variation with mill speed for different media shapes (J=15%)86 Figure 512 Power variation with mill speed for different media shapes (J=20%)87 Figure 513 Power variation with mill speed for different media shapes (J=25%)87 Figure 514 Variation of mill power draw with mill filling, J (cylpebs media)88EFFECTS OF GRINDING MEDIA SHAPES ON BALL MILL 2012年6月1日 ResearchGate Find and share researchResearchGate Find and share research2015年10月20日 When the charge volume of cylpebs is between 20% and 35% in the wet ball mill, cylpebs can be replaced by ceramic balls of the same single mass, with the total weight of the ceramic balls being (PDF) INVESTIGATION OF EFFECTS OF GRINDING MEDIA 2013年8月1日 In these mills, the grinding media and charge in a chamber are mobilized by a rotating internal agitator It is generally accepted that highly nonspherical debris from balls which break or spall due to manufacturing defects reduce ball mill grinding performance (Sinnott et al, 2011)Consumption of steel grinding media in mills – A review

Ball Mill Design/Power Calculation 911 Metallurgist
2015年6月19日 The approximate horsepower HP of a mill can be calculated from the following equation: HP = (W) (C) (Sin a) (2π) (N)/ 33000 where: W = weight of charge C = distance of centre of gravity or charge from centre of mill in feet a = dynamic angle of repose of the charge N = mill speed in RPM HP = A x B x C x L WhereME Elecmetal designs, manufactures and supplies the highest quality forged steel grinding media for SAG and ball mills in the world Our extensive field experience, engineering and consulting expertise enables us to accurately analyze operational data, so we can support our customers to achieve continuous improvement in their grinding processes The Grinding Media ME ElecmetalThe raw mill will be operate with a much coarser ball charge than the cement mill mainly because of the bigger slot sizes of the partition wall The transition zone consists of 50 mm and 60 mm balls The basis is a 50 mm ball size for 5% residue on the 4 mm sieve In case bigger grains are bypassing the partition through the center grate even Ball charge optimization INFINITY FOR CEMENT EQUIPMENT2022年1月30日 In terms of breakage mechanisms, while abrasion and impact prevail in ball mills, rod mills are used for their type of preferential grinding over larger particles In general, in the milling stage, The same pattern is observed when the media charge is varied, from 106 kWh/t to 78 kWh/t, which is a 25% reduction in energy, followed with Minerals Free FullText Rod Mill Product Control and Its 2011年10月1日 Recently, Clermont et al (2008) introduced the use of a set of sensors called Sensomag® It is basically a tool that allows simultaneous determination of slurry and media charge positions inside the mill Using the Sensomag®, they investigated the effect that changing the discharge configuration of a 48 m diameter ball mill has on power Effects of filling degree and viscosity of slurry on mill load
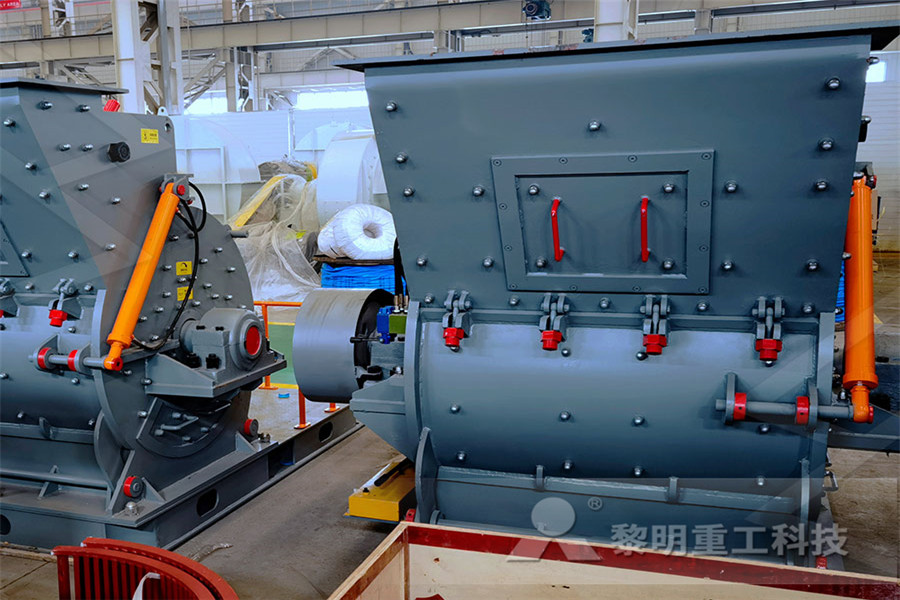
An overfilling indicator for wet overflow ball mills
2016年9月1日 The increased mill charge load will lead to an increase in mill power draw The onset point of overfilling an AG/SAG mill can be indicated when the mill power draw exceeds the safe operation power threshold In a ball mill, however, the mill power draw is dominated by ball media charge volume for a given mill rotational speed2017年2月13日 CERAMIC LINED BALL MILL Ball Mills can be supplied with either ceramic or rubber linings for wet or dry grinding, for continuous or batch type operation, in sizes from 15″ x 21″ to 8′ x 12′ High density ceramic linings of uniform hardness male possible thinner linings and greater and more effective grinding volumeBall Mills 911 Metallurgist2020年1月1日 The discharge end design of a ball mill plays an important role in discharging the desired particle sizes (−150 + 10 µm) and the percentage of recirculating load from the discharge end of the ball mill In continuous wet ball mills, the composition of feed (hard ore or soft ore) to the mill varies continuously, leading to uncontrolled A comparative study on a newly designed ball mill and the 2001年8月1日 Fig 2 shows the variation of the average torque and power with mill speed for the ball mill described above with a fill level of 50% The torque increases slowly until the peak is attained around N=80%As the amount of cataracting increases, the balance of the charge improves and the torque required to maintain the asymmetric charge position Charge behaviour and power consumption in ball mills: Key benefits High reliability – over a century of experience with 4000+ ball mills installed globally Large throughflow area ensures low pressure drop across the mill Horizontal slide shoe bearing design allows much simpler foundations and reduced installation height Increased effective grinding area with Stanex diaphragm designEnergy efficient cement ball mill from
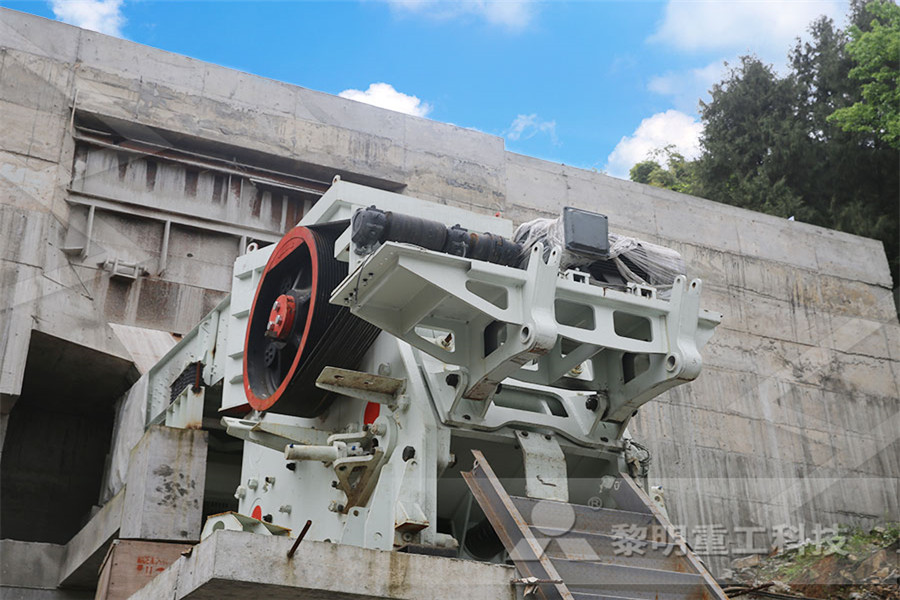
Modelling the influence on power draw of the slurry phase
2016年4月1日 In its original form Morrell’s model used a different media charge shape to that in Fig 1 (Morrell, 1992) and was configured to consider the cases where slurry was contained within the grinding charge as in a typical grate discharge AG/SAG mill (Fig 2a) or where it additionally formed a large slurry pool as occurs in all overflow ball mills 2018年1月1日 A planetary ball mill consists of a rotating sun disc (SUN), on which one up to four grinding chambers (GC) are located The grinding chambers themselves rotate at higher speeds, normally in opposite direction to the sun disc to ensure high forces and a highly random motion and collision pattern of grinding media (see Fig 1) Download : Dry grinding in planetary ball mills: Evaluation of a stressing 2019年2月1日 The ignition time (t ig) of the mechanically induced selfsustaining reaction (MSR) process involving the formation of TiB 2 from Ti/2B elemental mixtures was used to study the influence of the ratio (k = ω v /ω d) between the rotational speed of the supporting disc (ω d) and vials (ω v) on the milling efficiency of a Pulverisette 4 planetary millThe Effects of the speed ratio on the efficiency of planetary mills2016年9月1日 The increased mill charge load will lead to an increase in mill power draw The onset point of overfilling an AG/SAG mill can be indicated when the mill power draw exceeds the safe operation power threshold In a ball mill, however, the mill power draw is dominated by ball media charge volume for a given mill rotational speedAn overfilling indicator for wet overflow ball mills2020年10月22日 between temperature and mixing patterns The above literature mainly investigates the heat transfer behavior of hightemperature rotation body to granular material All of these provide an insight into the heat transfer phenomenon But the temperature rise caused by the charge motion has not been studied in ball millsAdvances in Mechanical Engineering 2021, Vol 13(3) 1–9

Ball mill media optimization Metcom Tech
2018年12月4日 Media charges were prepared by weighing and counting out the number of balls needed in each size class, determined by their individual weights and the specific gravity of steel Twentyseven equilibrium media charges are currently available for testing Examples are given in Table 1 The test mill feed is screen Media size testing apparatus 2011年2月1日 Conclusions The analysis of ball mill behaviour using DEM has been extended to include the coarse end of the fine powder particles in a laboratory scale ball mill This allows us to predict rather than deduce the effect of the powder on the overall flow and the effect of the flow and collisional environment on the fine particlesUnderstanding fine ore breakage in a laboratory scale ball mill 2021年1月1日 Monitoring mill load is vital for the optimization and control of grinding process This study proposed the use of an instrumented grinding media to assess solid loading inside a ball mill, with size and density of the instrumented ball comparable to that of the ordinary grinding mediaAn improved method for grinding mill filling ScienceDirect2022年1月1日 Note that the DEM simulations are only for the grinding media without considering the ground (fine) particles Compared to the grinding media, the number of ground particles is significantly less and the effect of the fine particles on the grinding media is insignificant [20,33] The motions of balls for different mill diameters are ConclusionsImpact energy of particles in ball mills based on DEM 2023年5月30日 80,70, and 60 mm Balls for D 33 e 1x Remainder of 1st Compartment Charge • D = Ball Dia, mm • Use “n” number of 50 and 40 mm Balls in 2nd Compartment (Transition Zone) • X = Distance from Transition Zone, m f Grinding Course: Ball Charge Design Methods PDF Scribd

ball mill media charge pattern horizonpaysan
2021年3月4日 Stirred media mills Stirred media mills are usually constructed in the form of a cylindrical drum inside which there are a series of rods, arms or perforated discs which are rotated on a central shaft The drum is loaded with grinding media, such as metal balls or glass sand The media and the charge is 'stirred' together and thus the 2017年4月29日 The original ball load in the mill was 6614 lb (3000 kg) and the load at the end of the 694 hr was 6338 lb (28748 kg) During this time, 590 lb (2676 kg) of balls less than 3 in (762 mm) in diameter were discarded from the mill The screen analysis of the ball charge at the end of the operation is shown in Table 20Grinding Media Wear Rate Calculation in Ball Mill 911 2013年3月15日 The Effect of Ball Size on the Energy Efficiency of Hybrid HighPressure Roll Mill/Ball Mill Grinding Powder Technology, Vol 105 , 1999, 199204 101016/S00325910(99)001382 in Google ScholarGrinding in Ball Mills: Modeling and Process Control Sciendo2022年1月1日 The ore charge was considered entrapped in between colliding balls which were subjected to the collision forces Flow patterns in ball mills with different sizes: (a) 127 mm; (b) 254 mm; (c) 508 mm; (d) 2000 mm; and (e) 3000 mm, when d = 254 mm, M* = 05 and N* = 06 sizes of ball mills were analysed to obtain the grinding rate of Impact energy of particles in ball mills based on DEM simulations The starting point for ball mill media and solids charging generally starts as follows: 50% media charge; Assuming 26% void space between spherical balls (nonspherical, irregularly shaped and mixedsize media will increase or decrease the free space) 50% x 26% = 13% free space; Add to this another 10%15% above the ball charge for total of 23% Ball Mill Media Charge Pattern pegourier
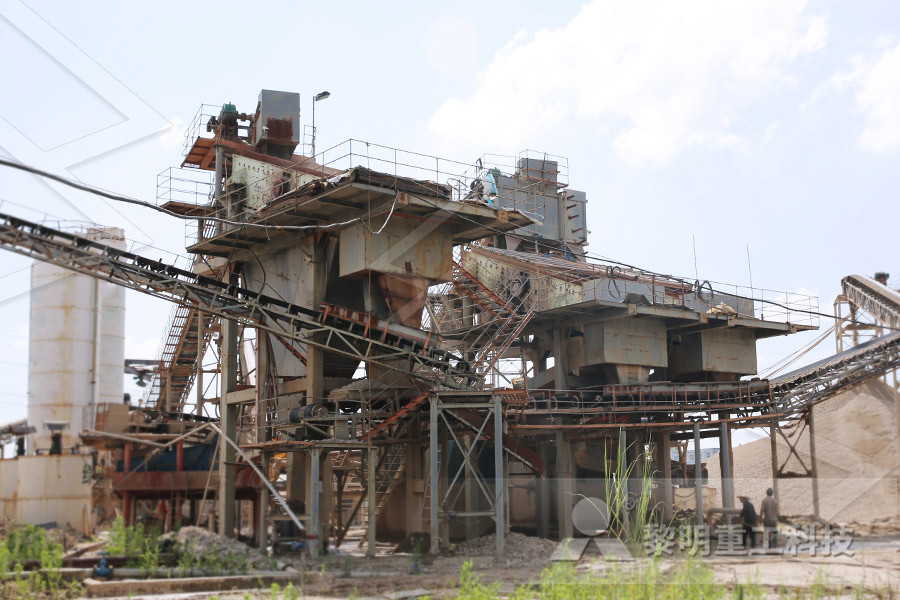
(PDF) Prediction of grindingmill power
1992年1月1日 The simulated charge motion using KMPC DEM in the 9 m Aerofall SAG mill and overall charge patterns obtained under the UV light are shown in Fig 8 30, 35 and 40% with ball media of 2 and 25 2020年8月25日 Mat circulating load factor is computed for rawmill and cementmill at a sep efficiency of 90 and 70% for target residue 16 and 1% respectively on 90 microns sieve This is observed, to maintain an acceptable circulating load factor between 15 to 20, a target mill discharge residue on 90 microns sieve would be 40–50 % for raw grinding and Grinding efficiency Ball mill by ASen MediumContribute to dihog/ development by creating an account on GitHub/ wet ball millmedia pattern in ball millsmd at main1 Introduction Highenergy ball milling is a complicated process employed in solid reactions for obtaining nanostructured materials, in powder form, with an average particle size of less than 100 nm The planetary mill is one of highenergy ball mills, which is used for efficient and precision millingModelling of the HighEnergy Ball Milling ProcessBall mill is the widely used comminution device for the size reduction of iron ore particles, yet the underlying mechan isms of heat transfer and thermal breakage inside the mills heretofore are Study on heat transfer behavior and thermal breakage

A cascadecataract charge flow model for power draft of tumbling mills
1992年9月1日 The mill charge actually tumbling is Me =Mmsml (27) Combining these expressions with eq 15 yields: Me 1 1 (28) M 7Zc J Similarly, the effective filling ratio becomes: Vc v Je (29) Vm V A CASCADECATARACT CHARGE FLOW MODEL FOR POWER DRAFT OF TUMBLING MILLS 17 where Vc is the total volume of the charge Modern ball mills consist of two chambers separated by a diaphragm In the first chamber the steelalloy balls (also described as charge balls or media) are about 90 mm diameter The mill liners are designed to lift the media as the mill rotates, so the comminution process in the first chamber is dominated by crushingBall Mill an overview ScienceDirect Topics2009年9月23日 the grinding media and the ball size distribution of the charge, is also discussed 22 Breakage mechan ism in tumbling ball mills Several mechanisms contribute to the grinding action that takes (PDF) Effect of ball size distribution on milling parametersStirred Mills – Ultrafine Grinding In Mineral Processing Design and Operations (Second Edition), 2016 1024 Operation of Vertical Mills Vertical stirred mills are usually charged with media occupying 80% of the mill volume which is in sharp contrast to tumbling mills that are seldom charged more than 40% of their volumes to allow space for the tumbling Stirred Mill an overview ScienceDirect Topics2018年10月15日 Ball Charge Management Deciding the Pattern Second Chamber – If the first chamber of the mill is achieving 2,5% residue on 1mm then there is no requirement for large media in the second chamber of a Day 1 5 BALL Mill Internals MBu PDF PDF

EFFECTS OF GRINDING MEDIA SHAPES ON BALL MILL
2021年7月27日 Figure 511 Power variation with mill speed for different media shapes (J=15%)86 Figure 512 Power variation with mill speed for different media shapes (J=20%)87 Figure 513 Power variation with mill speed for different media shapes (J=25%)87 Figure 514 Variation of mill power draw with mill filling, J (cylpebs media)年6月1日 ResearchGate Find and share researchResearchGate Find and share research2015年10月20日 When the charge volume of cylpebs is between 20% and 35% in the wet ball mill, cylpebs can be replaced by ceramic balls of the same single mass, with the total weight of the ceramic balls being (PDF) INVESTIGATION OF EFFECTS OF GRINDING MEDIA 2013年8月1日 In these mills, the grinding media and charge in a chamber are mobilized by a rotating internal agitator It is generally accepted that highly nonspherical debris from balls which break or spall due to manufacturing defects reduce ball mill grinding performance (Sinnott et al, 2011)Consumption of steel grinding media in mills – A review2015年6月19日 The approximate horsepower HP of a mill can be calculated from the following equation: HP = (W) (C) (Sin a) (2π) (N)/ 33000 where: W = weight of charge C = distance of centre of gravity or charge from centre of mill in feet a = dynamic angle of repose of the charge N = mill speed in RPM HP = A x B x C x L WhereBall Mill Design/Power Calculation 911 Metallurgist
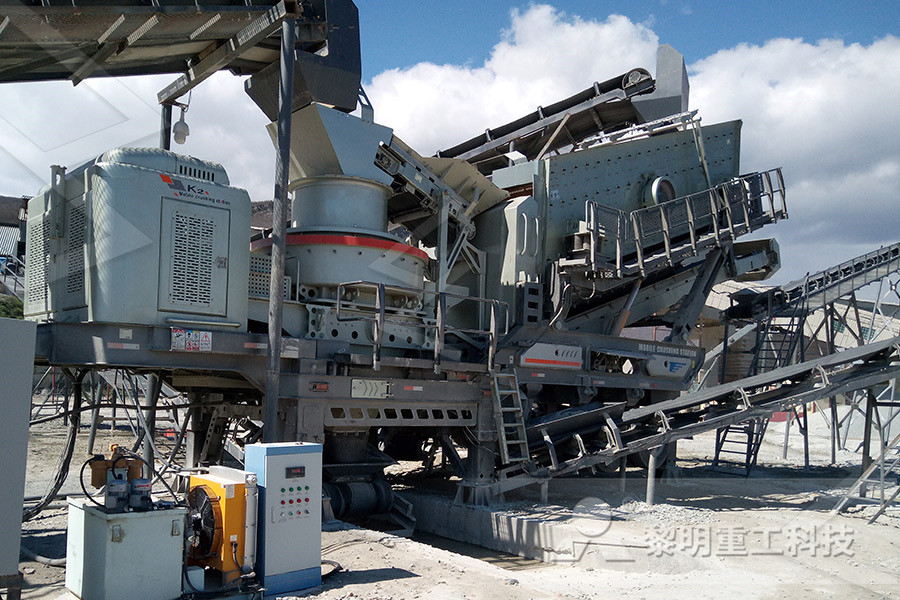
Grinding Media ME Elecmetal
ME Elecmetal designs, manufactures and supplies the highest quality forged steel grinding media for SAG and ball mills in the world Our extensive field experience, engineering and consulting expertise enables us to accurately analyze operational data, so we can support our customers to achieve continuous improvement in their grinding processesThe raw mill will be operate with a much coarser ball charge than the cement mill mainly because of the bigger slot sizes of the partition wall The transition zone consists of 50 mm and 60 mm balls The basis is a 50 mm ball size for 5% residue on the 4 mm sieve In case bigger grains are bypassing the partition through the center grate even Ball charge optimization INFINITY FOR CEMENT EQUIPMENT2022年1月30日 In terms of breakage mechanisms, while abrasion and impact prevail in ball mills, rod mills are used for their type of preferential grinding over larger particles In general, in the milling stage, The same pattern is observed when the media charge is varied, from 106 kWh/t to 78 kWh/t, which is a 25% reduction in energy, followed with Minerals Free FullText Rod Mill Product Control and Its