Grinding Media Distribution Stirred Media Mill
2022-10-29T05:10:05+00:00

Effects of axial grinding media distribution on the disc wear
2022年7月1日 Based on these insights, the grinding media in the stirred media mill are pressed into the holes of the discs, accelerated there to the local circumferential speed 2021年2月11日 Abstract Product fineness during grinding in stirred media mills is mainly influenced by the specific energy input, the stress energy Grinding Media Motion and Collisions in Different 2022年7月1日 As a result of the mechanical stress and the grinding media distribution depending on the operating parameters, horizontal stirred media mills have different Effects of axial grinding media distribution on the disc wear 2020年6月1日 This review describes stirred media mill technologies and operating principles, and summarises stress intensity theory which can be used for selecting Stirred media mills in the mining industry: Material 2021年2月1日 Fine grinding in stirred media mills is an important process in mineral, chemical and pharmaceutical industry The stressing mechanism in these mills is Experimental assessment of grinding bead velocity

Grinding Media Motion and Collisions in Different
2021年2月11日 The local grinding media concentration, velocity profiles, grinding media collisions and stress energies were compared for varied total grinding media fillings and stirrer speeds2020年6月1日 Grindability tests for stirred media mills By far the most common approach for estimating the energy requirements of industrial scale stirred media mills involve a Stirred media mills in the mining industry: Material 2021年4月1日 Each profile of particle size distribution obtained by 7 mm grinding media exhibited normal distribution (Fig 12 (b)) However, unlike the normal distribution, each Effect of grinding media properties and stirrer tip speed on 2019年1月1日 Fine grinding in stirred media mills is an important process in mineral, chemical and pharmaceutical industry The stressing mechanism in these mills is Determination of the axial grinding media distribution in the 2021年2月11日 mostly in the upper range of 70–90% However, continuous operation of a stirred mill can result in axially heterogeneously distributed grinding media, causing lower Grinding Media Motion and Collisions in Different Zones

Stirred media mills in the mining industry: Material
2020年5月1日 Stirred media mills are used by the mining industry for ultrafine grinding to enhance liberation, and to decrease particle sizes of industrial minerals to tailor functional properties2020年6月1日 Stirred media mills Efficient grinding of fine and ultrafine particles requires small media to increase the surface area and the consequent collision frequency, but ball mills are fundamentally limited in the momentum that can be applied to such small beads by the force of gravity, which sets a practical lower limit in media sizeStirred media mills in the mining industry: Material 2019年1月1日 When horizontal stirred media mills are used to grind highly concentrated slurries with a large throughput the grinding media tend to be pushed towards the product discharge This displacement may lead to hydraulic packing which has, in turn, negative consequences for the grinding process like ineffective energy utilisation and increased Determination of the axial grinding media distribution in the 2020年6月1日 Stirred media mills are used by the mining industry for ultrafine grinding to enhance liberation, and to decrease particle sizes of industrial minerals to tailor functional properties This review describes stirred media mill technologies and operating principles, and summarises stress intensity theory which can be used for selecting efficient Stirred media mills in the mining industry: Material 2021年1月8日 Fine grinding in stirred media mills is an important process in mineral, chemical and pharmaceutical industry The stressing mechanism in these mills is grinding through compression and shearing Experimental assessment of grinding bead velocity
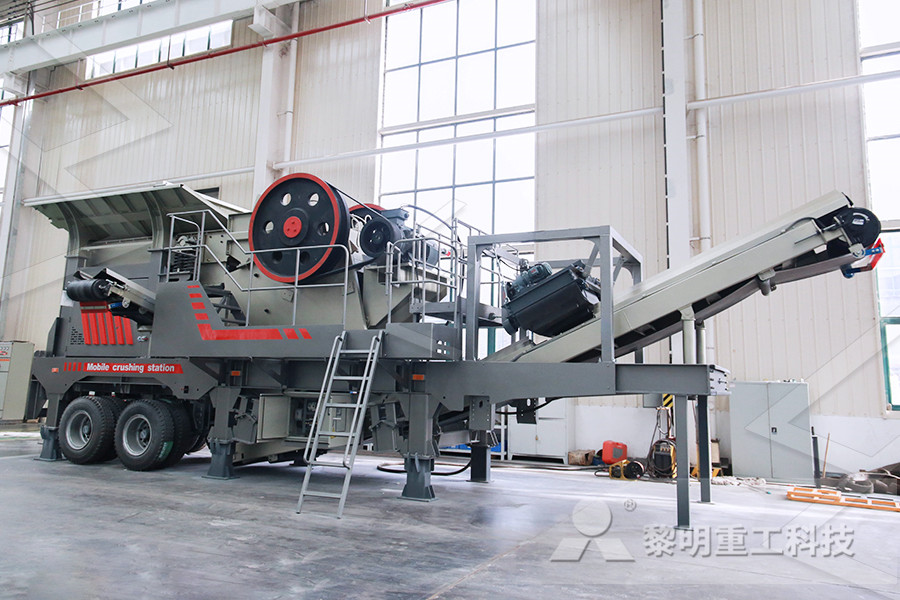
Effects of axial grinding media distribution on the disc wear
2022年7月1日 Wetoperated stirred media mills are commonly used in the field of fine and ultrafine grinding Depending on the application, there are different mill geometries and millequipmentmaterials of 2021年7月1日 The work uses the UFRJ mechanistic mill model and DEM to analyze the effect of several design and operating variables on the apparent breakage rates and breakage distribution function of a batch gravityinduced stirred mill grinding copper oreIt shows that breakage rates increase significantly with stirrer speed; that increase in Predicting the effect of operating and design variables in grinding 2021年2月11日 Abstract Product fineness during grinding in stirred media mills is mainly influenced by the specific energy input, the stress energy transferred by the colliding grinding media and the stress Grinding Media Motion and Collisions in Different Zones of Stirred 2021年2月11日 mostly in the upper range of 70–90% However, continuous operation of a stirred mill can result in axially heterogeneously distributed grinding media, causing lower local filling levels Moreover, the stirrer tip speed was varied between 6 and 14 m/s, corresponding to between 1592 and 3714 rpm, respectively The local grinding media Grinding Media Motion and Collisions in Different Zones 2001年3月1日 Section snippets Comminution of limestone Limestone with a median particle size x 50 of 60 μm was comminuted in discontinuous experiments in a stirred media mill (PM5 of Draiswerke, Mannheim) with a grinding chamber net volume of 56 l Fig 2 shows the grinding chamber of the mill For cooling purposes the grinding chamber is Stress intensity in stirred media mills and its effect on
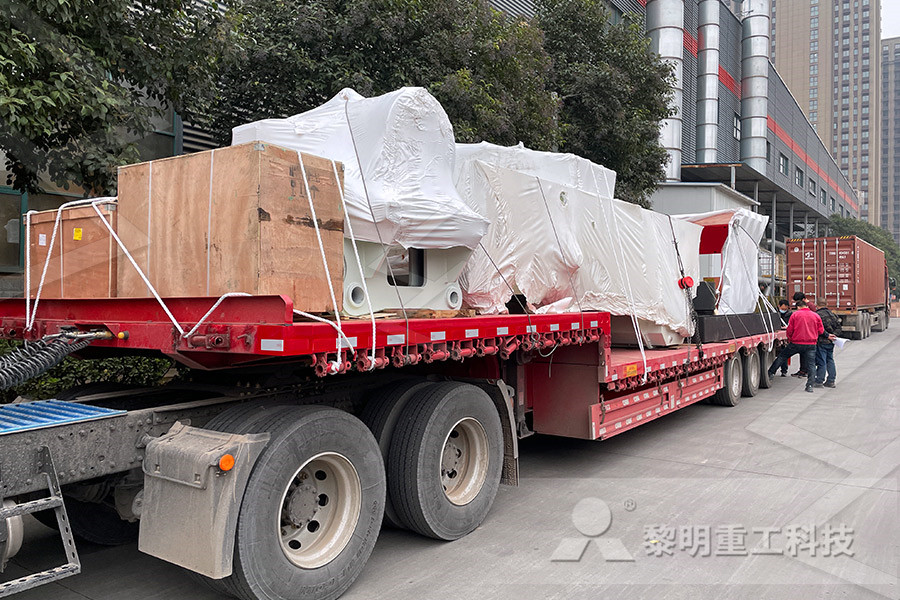
Stress energy distribution in different stirred media mill
2004年12月10日 Section snippets Millrelated stress model For a better description of the physical processes in stirred media mills and in order to look at a stirred media mill not as a black box, at the Institute of Mechanical Process Engineering of the Technical University of Braunschweig, the socalled stress models were developed (see Bunge, 1992, Kwade, 2021年1月9日 media, slurry, and mill structure in a pilot wet stirred media mill (Outotec HIG5) with 75 kW of installed power The mill structure is modeled with FEM, grinding media(PDF) A Novel ParticleBased Approach for Modeling a Wet 2022年2月28日 Many investigations have been carried out on cement grinding using stirred mills [119,120,121] It has been concluded that using stirred mills can reduce energy consumption by 7–18% MaxxMill, for instance, is a stirred media mill that has successfully been utilized in dry mineral processing The main parts of a MaxxMill are a revolving Grinding SpringerLink2023年1月31日 Varied types/geometries of stirred mills have been produced by different manufacturers, and the comparison task has been accomplished for some of the technologies, ie, Tower mill vs IsaMill However, the main drawbacks of these comparisons were the uncommon characteristics of the milling environment, such as media size In Performance Comparison of the Vertical and Horizontal Oriented Stirred 2007年10月19日 The role of slurry rheology in stirred media milling of quartzite has been investigated by varying important grinding parameters such as media bead density and size, addition of chemicals, solids concentration, stirrer rotational speed as well as the combined effect of these factors Media bead density has an evident but complex effect on stirred Influence of slurry rheology on stirred media milling of quartzite
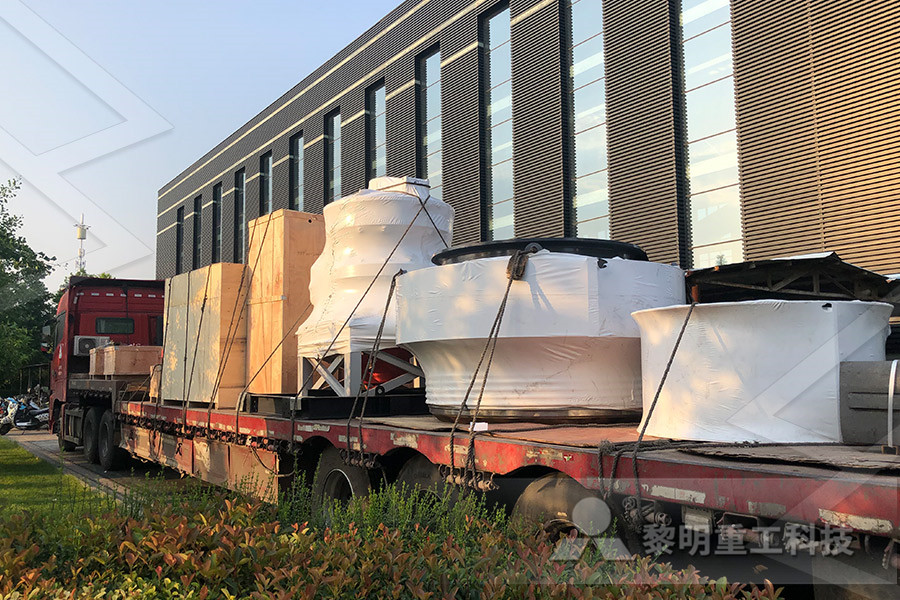
XMOL
2021年2月11日 The stress energy from grinding media collisions is heterogeneously distributed in stirred media mills Herein, in order to characterize the stress energy distribution and the local grinding media collision frequencies, the grinding media motion was calculated using discrete element method (DEM) simulations coupled with computational 2013年1月1日 The effect of the operational parameters of a stirred media mill on the particle size of pigment TiO 2 and the width of its particle size distribution was studied here with the aim of obtaining a particle size of 03 μm and as narrow a width of the particle size distribution as possible Fine grinding was performed using a laboratoryscale Effect of operational parameters and stress energies on the 2022年9月16日 Wetstirred media milling was employed and values of the parameters involved have been chosen effectively for an improved grinding process Nanoparticles of the biomaterials were prepared successfully after 60 min of milling, with horizontal mill providing higher rate of particle breakage as compared to vertical millOptimized Nanomilling of Biomaterials by WetStirred Media Didier Schons Arno Kwade The IsaMill is an often used type of wet operated stirred media mills in mining and minerals industry Thus usually mill sizes of several cubic meters are used in the Didier Schons's research works2022年7月1日 In the case of stirred media mills, wear occurs most frequently on the stirrer and the mill liner, besides the grinding media which show the highest wear (Becker, 1999)Due to high throughputs combined with mostly high solids concentrations of the slurry usually desired for productionscale plants, the grinding media tend to be transported Effects of axial grinding media distribution on the disc wear
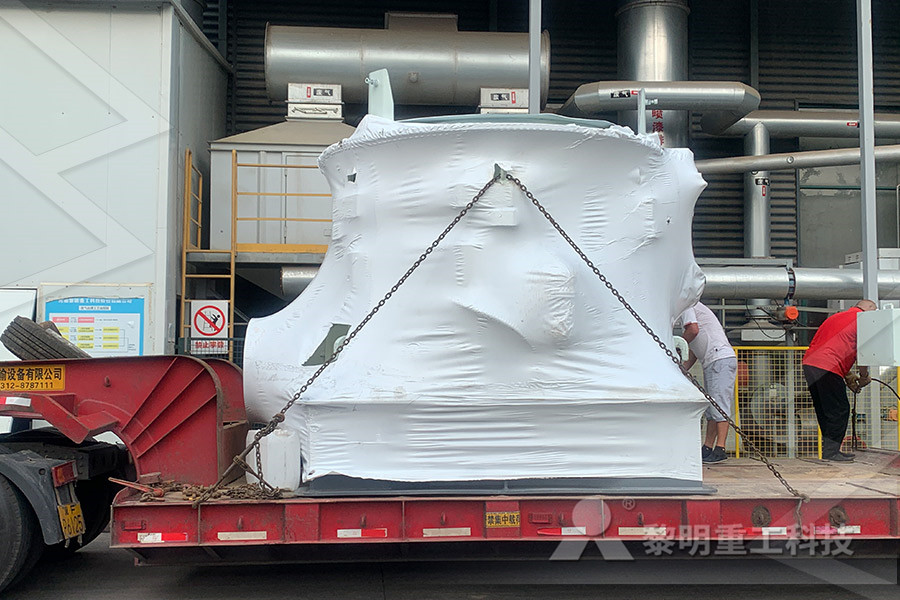
Theoretical and experimental investigation on particle and
1999年11月1日 Stirred media mills are used in various industries for comminution Generally they are operated with a fluid, usually a liquid, grinding beads and feed particles leading to a multiphase flow problem The motion in the stirred media mill is invoked by stirrers that are fitted with disks or pins driving the flow2022年1月1日 The laboratoryscale stirred mill specifications and experimental conditions conducted in the test are shown in Table 1The mass of grinding media (m GM) and feed (m P) was added into the grinding chamber of the stirred mill using the following formulae below, respectivelyFormulae can be expressed as, (4) m GM = V × J × ρ GM × 062 (5) Effect of operating conditions on the particle size distribution 2022年1月1日 The laboratoryscale stirred mill specifications and experimental conditions conducted in the test are shown in Table 1 The mass of grinding Effect of grinding media diameter The stirrer tip speed of 2 m/s, media filling rate of 100%, and powder filling rate of 05 were used in the experiment to investigate the influence of grinding media Effect of operating conditions on the particle size distribution 2017年4月1日 The interactions between slurry, grinding media and mill structure are modelled by twoway couplings between the PFEM, the DEM and the FEM models The coupled model of the present study is used to predict the motion of slurry and grinding media, and to calculate the power draw during wet comminution in a pilot scale horizontal Estimation of product relating energy of wet operated stirred media 2018年12月1日 It has been reported in the literature that the smaller grinding media used in stirred mills increases the contact probability between the media and the particles, and, therefore, the number of stress events inside the mill should also increase (Matter, 1983, Mankosa et al, 1986, Erdem and Ergun, 2009, Katubilwa and Moys, 2009)Predicting the product particle size distribution from a

Choosing the Best Media Mill For Your Wet Grinding Application
2003年7月1日 The ability to operate a mill with smallerdiameter grinding media greatly increases the mill's efficiency and can overall further increase the quality of product through finer grinding Dr Stehr, Norbert (1984), Residence Time Distribution in a Stirred Ball Mill and Their Effect on Comminution", DRAIS News Vol 1, No 2 SinglePass 2021年4月21日 31 Vertically Oriented Stirred Mill Tests Based on grinding results from wet stirred milling, the stress energy in stirred media mills is mainly determined by the operating parameters of the tip speed of the stirrer and the size, density and Young’s modulus of the grinding mediaThe Influence of Stirred Mill Orientation on Calcite Grinding2023年7月10日 The present literature review explores the energyefficient ultrafine grinding of particles using stirred mills The review provides an overview of the different techniques for size reduction and the impact of energy requirements on the choice of stirred mills It also discusses the factors, including the design, operating parameters, and feed material EnergyEfficient Advanced Ultrafine Grinding of Particles Using Stirred 2021年3月15日 A grinding technology should consider the physical properties of the material, ie, size, shape, which have effects on the product specifications, ie, quality, strength or overall process efficiency In this respect, this study aimed at evaluating the variations in the shape of product size distribution of a stirred media mill as the attention Impacts of process and design conditions of dry stirred 2021年3月15日 Certainly, the internal geometry of the dry stirred media mill is important for the efficiency of grinding and its product characteristics (Altun et al, 2014) as it is well known for wet stirred media milling (Kwade and Schwedes, xxxx, Kwade and Schwedes, 1997), in which the stress energy distribution decides about the size distribution width Impacts of process and design conditions of dry stirred
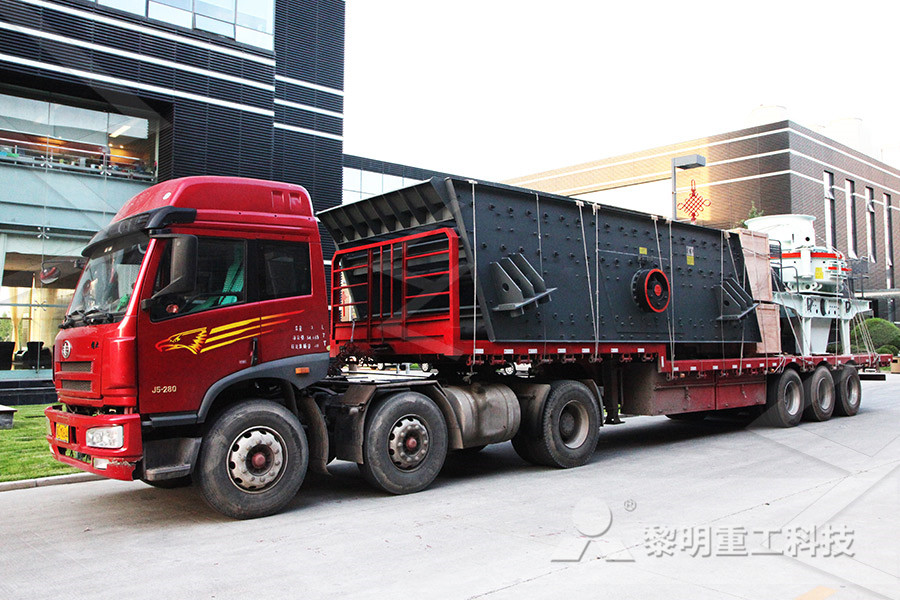
Experimental assessment of grinding bead velocity
2021年1月8日 DOI: 101016/JAPT202012022 Corpus ID: ; Experimental assessment of grinding bead velocity distributions and stressing conditions in stirred media mills @article{Bttcher2021ExperimentalAO, title={Experimental assessment of grinding bead velocity distributions and stressing conditions in stirred media mills}, author={AnnChristin 1975年7月1日 The attrition mill is a device for mechanically reducing solid particle size by intense agitation of a slurry of material being milled and coarse milling media For example, in 10 hours of milling, specific surfaces of 40 and 25 m 2 /g were obtained for alumina and barite, corresponding to 38 and 56 nm equivalent spherical diameter, respectivelyAttrition mill operating characteristics ScienceDirect2021年2月1日 The stressing mechanism in these mills is grinding through compression and shearing by grinding beads A few studies have examined grinding bead transport in stirred media mills Radiometric methods detect the local filling degree, but little is known about the experimental motion of the grinding beads in the millExperimental assessment of grinding bead velocity 2015年10月1日 Wet stirred media mills are widely used in many industries, and the mills' operation is studied for different materials, including CaCO 3 [20], titanium dioxide (TiO 2) [21], and fused corundum [22] Wet stirred media mills make it possible for particles to be ground down to their theoretical grinding limit [20], [23], [24]Effect of operational parameters and stress energies on stirred media 1999年11月1日 The comminution process in a stirred media mill is usually determined by 1 how often each feed particle (and the fragments arising from the feed particle) is stressed (number of stress events) and 2 how high the stress intensity at each stress event is Since the movement of grinding media and product particles is a statistical process, in Wet comminution in stirred media mills ScienceDirect
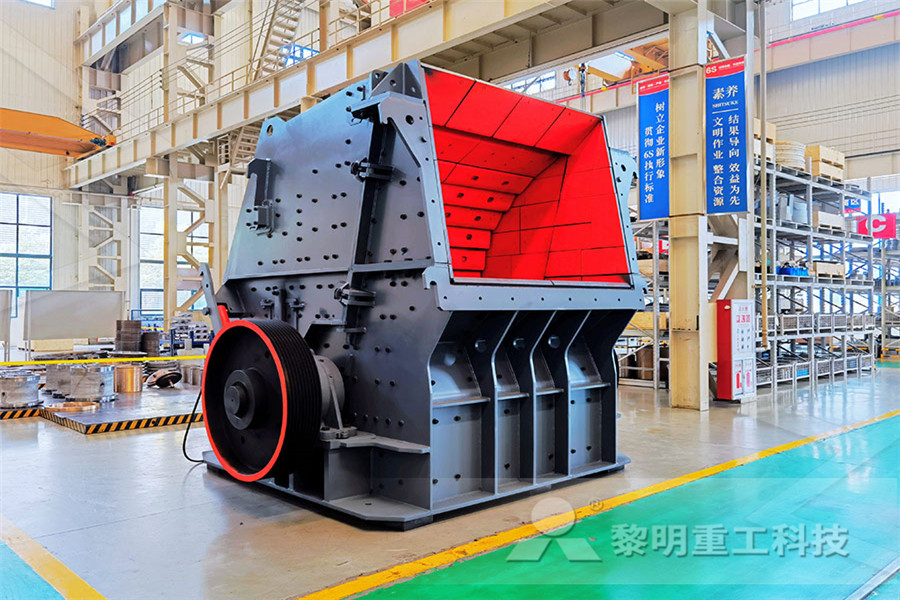
The shape of product size distributions in stirred mills
2006年12月1日 Stirred media mills, also referred to as stirred ball or stirred bead mills, generally have a good ability to produce fine particles with a relatively narrow particle size distribution Wet grinding with vertical stirred ball mills is typically carried out for slurries containing particles smaller than 200 μm, such as industrial minerals and 2021年2月11日 Product fineness during grinding in stirred media mills is mainly influenced by the specific energy input, the stress energy transferred by the colliding grinding media and the stress frequency The stress energy from grinding media collisions is heterogeneously distributed in stirred media mills Herein, in order to characterize the Grinding Media Motion and Collisions in Different Zones of Stirred Modeling of wet stirred media mill processes is challenging since it requires the simultaneous modeling of the complex multiphysics in the interactions between grinding media, the moving internal agitator elements, and the grinding fluid In the present study, a multiphysics model of an HIG5 pilot vertical stirred media mill with a nominal power of 75 A Novel ParticleBased Approach for Modeling a Wet Vertical Stirred 2016年12月10日 The demand for everdecreasing grinding fineness has resulted in the replacement of traditional ball mills with stirred media mills, which make possible the needed drastic increase in energytransfer intensity along with the required decrease in the grinding media size A stirred media mill is a high energy density mill which is used for Application of the product related stress model for product 2004年12月10日 A stress energy of 0001 SE GM and higher occurs in about 55% of the total grinding chamber volume in the smallest grinding chamber Whereas this and higher stress energies can be found in only 40% of the total volume of the grinding chamber of the medium size mill and in only 22% of the volume of the largest millStress energy distribution in different stirred media mill

Stirred media mills in the mining industry: Material
2020年5月1日 Stirred media mills are used by the mining industry for ultrafine grinding to enhance liberation, and to decrease particle sizes of industrial minerals to tailor functional properties2020年6月1日 Stirred media mills Efficient grinding of fine and ultrafine particles requires small media to increase the surface area and the consequent collision frequency, but ball mills are fundamentally limited in the momentum that can be applied to such small beads by the force of gravity, which sets a practical lower limit in media sizeStirred media mills in the mining industry: Material 2019年1月1日 When horizontal stirred media mills are used to grind highly concentrated slurries with a large throughput the grinding media tend to be pushed towards the product discharge This displacement may lead to hydraulic packing which has, in turn, negative consequences for the grinding process like ineffective energy utilisation and increased Determination of the axial grinding media distribution in the 2020年6月1日 Stirred media mills are used by the mining industry for ultrafine grinding to enhance liberation, and to decrease particle sizes of industrial minerals to tailor functional properties This review describes stirred media mill technologies and operating principles, and summarises stress intensity theory which can be used for selecting efficient Stirred media mills in the mining industry: Material 2021年1月8日 Fine grinding in stirred media mills is an important process in mineral, chemical and pharmaceutical industry The stressing mechanism in these mills is grinding through compression and shearing Experimental assessment of grinding bead velocity
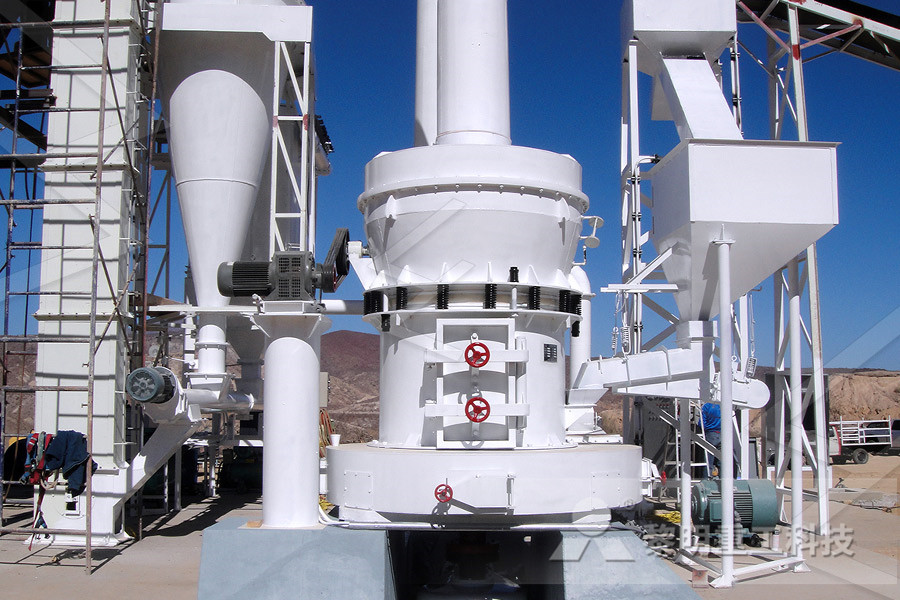
Effects of axial grinding media distribution on the disc wear
2022年7月1日 Wetoperated stirred media mills are commonly used in the field of fine and ultrafine grinding Depending on the application, there are different mill geometries and millequipmentmaterials of 2021年7月1日 The work uses the UFRJ mechanistic mill model and DEM to analyze the effect of several design and operating variables on the apparent breakage rates and breakage distribution function of a batch gravityinduced stirred mill grinding copper oreIt shows that breakage rates increase significantly with stirrer speed; that increase in Predicting the effect of operating and design variables in grinding 2021年2月11日 Abstract Product fineness during grinding in stirred media mills is mainly influenced by the specific energy input, the stress energy transferred by the colliding grinding media and the stress Grinding Media Motion and Collisions in Different Zones of Stirred 2021年2月11日 mostly in the upper range of 70–90% However, continuous operation of a stirred mill can result in axially heterogeneously distributed grinding media, causing lower local filling levels Moreover, the stirrer tip speed was varied between 6 and 14 m/s, corresponding to between 1592 and 3714 rpm, respectively The local grinding media Grinding Media Motion and Collisions in Different Zones 2001年3月1日 Section snippets Comminution of limestone Limestone with a median particle size x 50 of 60 μm was comminuted in discontinuous experiments in a stirred media mill (PM5 of Draiswerke, Mannheim) with a grinding chamber net volume of 56 l Fig 2 shows the grinding chamber of the mill For cooling purposes the grinding chamber is Stress intensity in stirred media mills and its effect on