Grinding Efficiency Of Ball Mill Calculating Equation
2023-08-09T02:08:20+00:00

Grinding efficiency of ball mill calculating equation NEWS
2023年9月10日 How to calculate the grinding efficiency of ball mills? Ball mill grinding efficiency can be calculated using the following equation: Efficiency = (100% Productivity) * 100 Efficiency = Ball mill grinding efficiency Productivity = Ball mill output per hour % 2018年12月9日 Ball mill = coarse particles (in the plant ball mill) grinding efficiency Ore grindability (in the lab ball mill) The units of "ball mill grinding efficiency" will be covered in MODULE #5: FUNCTIONAL PERFOMANCE OF BALL 2018年4月20日 The first two Grinding Efficiency Measurement examples are given to show how to calculate Wio and Wioc for single stage ball How to Measure Grinding Efficiency 911 2016年1月1日 To improve the efficiency of a ball grinding the ball mills are transferred in closed circuit with airseparators of various designs In the article the analysis of existing grinding(PDF) Analysis of the efficiency of the grinding 2002年11月1日 Schellinger's calculated ball mill efficiency, in dry or wet ball mill grinding, ranges between 10% and 19%, with the higher figure occurring at the optimal mill The energy efficiency of ball milling in comminution

Quantifying the energy efficiency of fine grinding
2021年11月25日 In fact, in four of the surveys, the SAG mill was found to be more efficient at producing circuit product than the ball mill Similar results have been seen consistently across all the surveys where this 2021年1月22日 Based on the specific productivity and grinding efficiency, the appropriate grinding parameters were ascertained as follows: material ball ratio of 07, ceramic ball An innovative approach for determining the grinding media 2022年1月1日 Abstract The size of grinding media is the primary factor that affects the overall milling efficiency of a ball mill (eg power consumption and particle size Effect of grinding media on the milling efficiency of a ball mill1989年1月1日 The grindingproduct size, P, in a Bond ball mill, which is given by the aperture size which passes 80% of the grinding product as a function of the aperture size Calculation of energy required for grinding in a ball mill2002年11月1日 Since the energy required to produce such a product ranges from 10 to 100 kWh/t in real grinding systems, the calculated energy efficiency would be 01–1% The energy efficiency of ball milling in comminution

Ball Mill an overview ScienceDirect Topics
where d bmax is the maximum size of feed (mm); σ is compression strength (MPa); E is modulus of elasticity (MPa); ρb is density of material of balls (kg/m 3); D is inner diameter of the mill body (m) Generally, a maximum allowed ball size is situated in the range from D /18 to D/24 The degree of filling the mill with balls also influences productivity of the mill 2020年12月17日 With ballmill grinding being one of the most energyconsuming techniques, setting the optimal values of the operational and mineralogical parameters for efficient grinding is a key target in mineral processing plants [6,7,8,9,10] Ball size is one of the key factors of ballmill efficiency [11,12], and may have a significant financial impact Kinetics of DryBatch Grinding in a LaboratoryScale Ball Mill 2023年10月18日 You need a twostage solution, first stage opencircuit mill and then second stage closedcircuit mill First stage, will be broken into two parts as well, you use a Bond rod mill work index for the coarse component of the ore (+21 mm) and the Bond ball mill work index for the fine component (21 mm)Bond Work Index (Energy equation) Grinding Classification Circuits 2018年12月9日 equation for ball mill circuits • Define and calculate the classification system efficiency of a ball mill circuit • Define and calculate the grinding efficiency of the ball mill in a ball mill circuit • Relate overall ball mill circuit output and circuit efficiency to specific design and operating variablesMODULE #5: FUNCTIONAL PERFOMANCE OF BALL Grinding tests were conducted using a pearshaped ball mill on an oxidized coppercobalt ore to determine the milling parameters Twelve monosized fractions of the ore sample were prepared and Ball mill characteristics and test conditions Mill Diameter, D
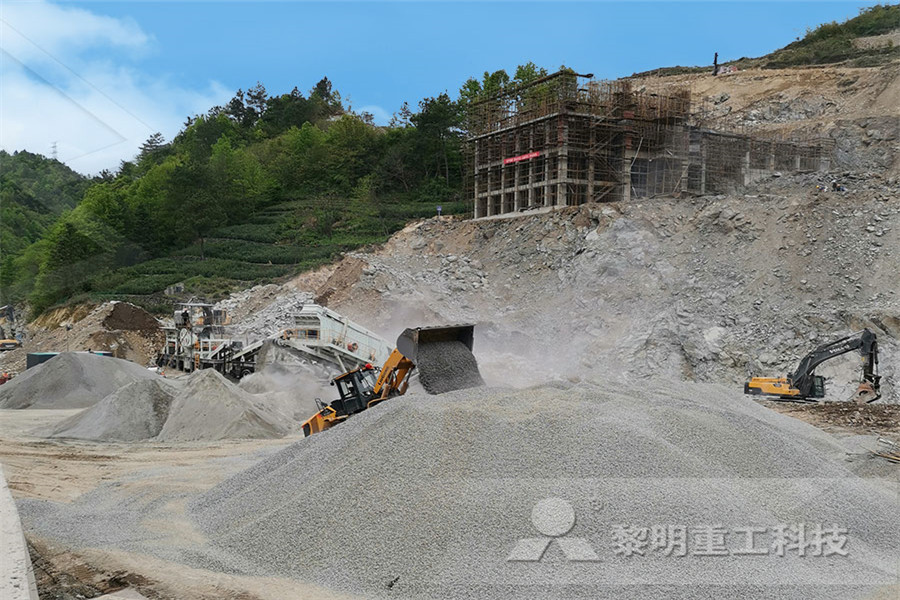
Closed circuit ball mill – Basics revisited ScienceDirect
2013年4月1日 Introduction Over the years, ball mill circuits closed with cyclones have become an industry standard, and since the early days, it has been recognised that classification efficiency and circulating load both have a major effect on the efficiency of closed circuit grinding (ie its capacity to produce the desired final product)2015年6月19日 A Ball Mill Critical Speed (actually ball, rod, AG or SAG) is the speed at which the centrifugal forces equal gravitational forces at the mill shell’s inside surface and no balls will fall from its position onto the shell The imagery below helps explain what goes on inside a mill as speed varies Use our online formula The mill speed is typically defined Ball Mill Critical Speed 911 Metallurgist2013年7月15日 In the standard AC closed circuit ball mill grindability test the work index is found from where Pi is the opening in microns of the sieve mesh tested, and Gbp is the net grams of mesh undersize produced per revolution of the 12″ x 12″ test ball mill The closed circuit 80% passing size P averages P1/log 20 for all sizes larger than 150 meshBond Work Index FormulaEquation 911 Metallurgist2002年11月1日 The effect of ball load composition, by varying the grinding media size distribution (eg alternatively by mixing four groups of 195, 38 mm; 195, 50 mm; 38, 50 mm and 195, 38, 50 mm), on the The energy efficiency of ball milling in comminution2020年2月18日 The rotation speed of a mill is an important factor related to its operation and grinding efficiency Analysis and regulation of the optimal speed under different working conditions can effectively reduce energy loss, improve productivity, and extend the service life of the equipment However, the relationship between the optimal speed and different Optimal Speed Control for a SemiAutogenous Mill Based on Discrete
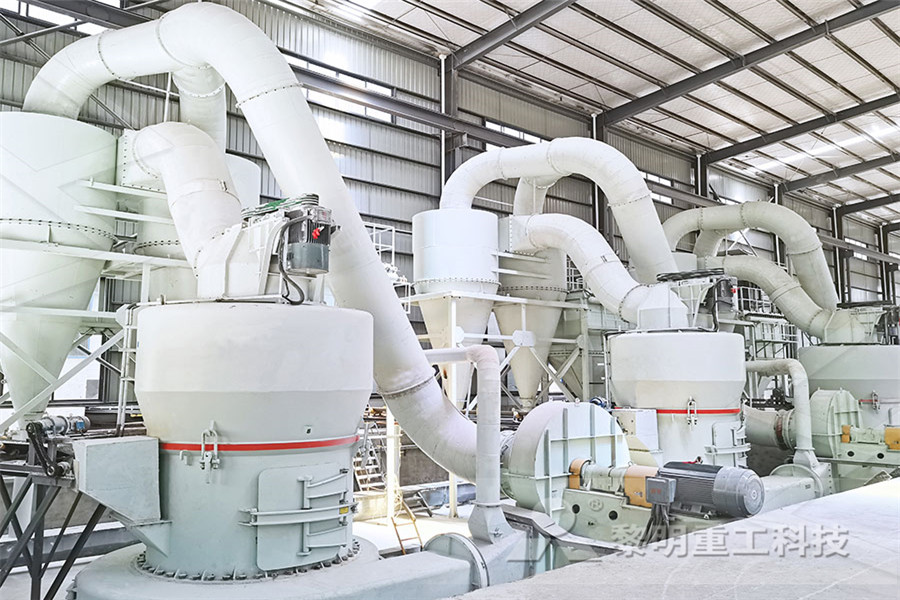
An innovative approach for determining the grinding media
2021年1月22日 Introduction Grinding operation is used extensively in the industry of beneficiation, metallurgy, chemical engineering, and electric power Assisted by the impact and abrasion between media (steel ball, steel rod, gravel, ceramic ball) and ore, the grinding operation reduces the particle size in the mill [[1], [2], [3]]2019年8月30日 V — Effective volume of ball mill, m3; G2 — Material less than 0074mm in product accounts for the percentage of total material, %; G1 — Material less than 0074mm in ore feeding accounts for 0074mm in the percentage of the total material, %; q’m — Unit productivity calculated according to the new generation grade (0074mm), t/(m3h) The Ball Mill Parameter Selection Calculation JXSC2020年9月24日 and the Morrell equations and their application (see Annex B) A worked example is provided in Annex C 5 SCOPE The Morrell method can be used to predict the specific energy of comminution circuits, where such circuits include combinations of any of the following equipment: • Autogenous Grinding (AG) and SemiAutogenous Grinding Morrell MethodGMGICEv01r01 Morrell 31 May 2023; The grinding efficiency of a ball mill can be calculated using the following equation: Grinding Efficiency = (Gross Discharge Rate of Fines) / (Net Discharge Rate of Fines) The gross discharge rate of fines refers to the rate at which the fine particles exit the mill, while the net discharge rate of fines is the rate at which the fine particles are being Grinding efficiency of ball mill calculating equation2020年7月2日 In total, 165 scenarios were simulated When the mills charge comprising 60% of small balls and 40% of big balls, mill speed has the greatest influence on power consumption When the mill charge is more homogeneous size, the effect of ball segregation is less and so the power consumption of the mill will be less affectedEffects of Ball Size Distribution and Mill Speed and Their Interactions

A Comparative Study of Energy Efficiency in Tumbling Mills with
An evaluation of Relo grinding media (RGM, Reuleaux tetrahedronshaped bodies) performance versus standard grinding media (balls) was made through a series of grinding tests, including a slight modification of the standard Bond test procedure Standard Bond tests showed a reduction in the Bond ball mill work index (wi) of the mineral sample used 2020年2月18日 The rotation speed of a mill is an important factor related to its operation and grinding efficiency Analysis and regulation of the optimal speed under different working conditions can effectively reduce energy loss, improve productivity, and extend the service life of the equipment However, the relationship between the optimal speed and different Optimal Speed Control for a SemiAutogenous Mill Based on Discrete 2021年1月1日 The fraction of mill volume occupied by rocks, grinding media and slurry in grinding mills are dominant factors influencing AG and SAG mill power draw and grinding rate Hence accurate mill filling measurements are needed for modelling mills To that end, it is usually necessary to enter the confined space of a grinding mill, a task that An improved method for grinding mill filling measurement and 2022年1月30日 The aim of this study is to evaluate the effect that the size of grinding media exerts on ferronickel slag milling efficiency and energy savings A series of tests were performed in a laboratory ball mill using (i) three loads of single size media, ie, 40, 254, and 127 mm and (ii) a mixed load of balls with varying sizes In order to simulate the Effect of Grinding Media Size on Ferronickel Slag Ball Milling 2022年1月1日 The size of grinding media is the primary factor that affects the overall milling efficiency of a ball mill (eg power consumption and particle size breakage) This article tackles the lack of a Effect of grinding media on the milling efficiency of a ball mill
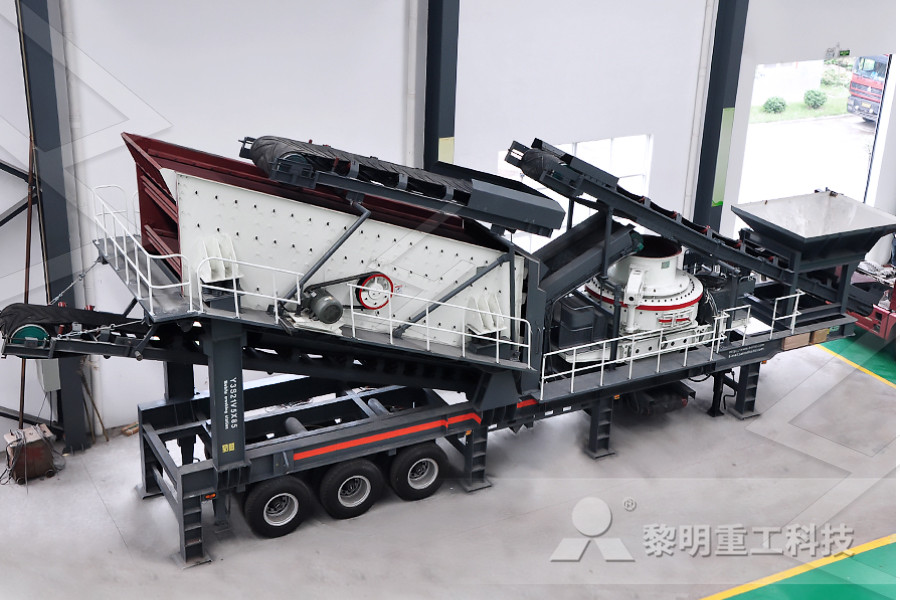
Efficiency and grinding media filling level IEEE Conference
2013年4月19日 Slide shoe supported mills eased those concerns and made possible the lowering of “normal” filling levels of 40% to 45% to a new “normal” of 28% to 35% Ten to fifteen years ago two events took place which seemed to support the results of the preliminary investigations of low level filling and efficiency In the first case, one of the 1989年1月1日 The grindingproduct size, P, in a Bond ball mill, which is given by the aperture size which passes 80% of the grinding product as a function of the aperture size of the test screen Pk, can be expressed by the formula P= P k K 2 These functions for G and P enable us to calculate the value of Wi for any other size of grinding product if we know Calculation of energy required for grinding in a ball mill2015年11月1日 Section snippets Review of grinding and ball wear models Austin et al [3] proposed a grinding circuit model (Eq (1)), which comprises a mathematical description of a continuous grinding in open circuit from which the general sizemass balance equation applicable to the particle size reduction process was derived: p i = w i τ = ∑ j = 1 i d i, j f Ball size distribution for the maximum production of a the energy efficiency, indicating that using small diameter bead was effective for efficient grinding 1 Introduction Although milling operation had been a wellknown unit operation, it often held a prominent position in the industry up until today Therefore, number of types of grinder had been developed to fulfil the demands of theStudy on the Effects of Grinding Factor and Scaling up in 2016年12月12日 If P is less than 80% passing 70 microns, power consumption will be Ball Mill Power Calculation Example A wet grinding ball mill in closed circuit is to be fed 100 TPH of a material with a work Ball Mill Design/Power Calculation LinkedIn
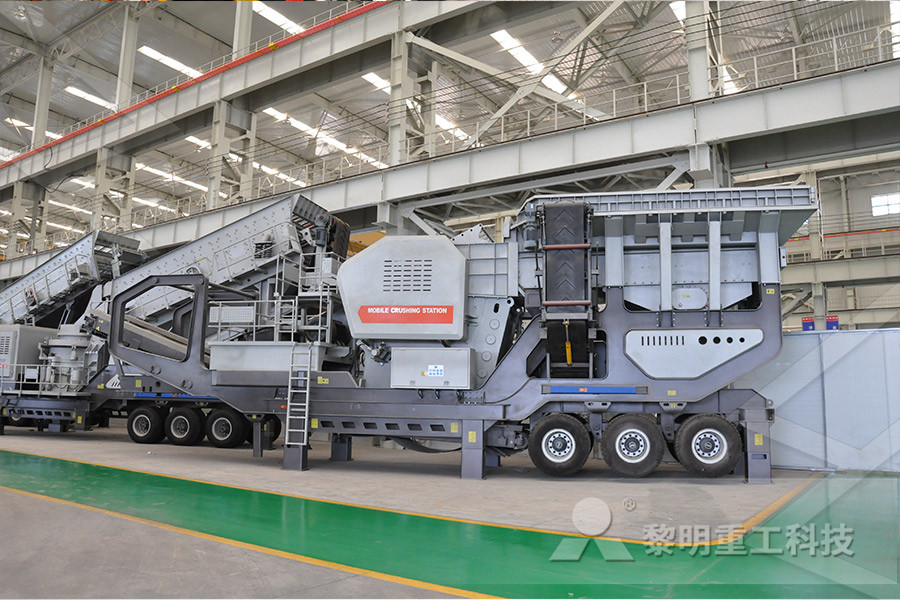
Ball mill abrasion test (BMAT): Method development and
2022年1月1日 Introduction The ball mill abrasion test (BMAT) is an industriallyrelevant multipurpose wear test method that enables tribologists and abrasion scientists to study the abrasive wear behaviour of materials for various service applications, particularly for grinding balls and mill liners, under conditions and contact mechanics very similar to the industrial 2018年2月20日 Bond Grinding Circuit Efficiency • The Bond Work Index equation • Ore test WI Example SAGBall Mill Circuit WI Efficiency Calculation • Bond Test WI’s (kWh/t): Crushing:160 Rod Mill: 145 Ball Mill: 138 SS ball mills, Rowland 1998 87% 115 x Ball mills: Rodball, Selbaie, McIvor 1988 100% 10 x Bond Grinding Circuit Efficiency ceecthefuture2021年2月8日 Abstract Ball drum mills (BDM) are one of the main types of coalgrinding equipment in Russia A significant drawback of BDM is high power consumption (a significant part of the TPP’s own needs) With a huge scale of production, reducing these costs even by a few percent gives a significant economic effect The problem of Determining Optimum Productivity of a Ball Drum Mill When Keep operation in a good efficiency Conventional grinding system Main Machine 1 Feeding system 2 Tube mill 3 Dynamic separator Maximum steel ball size (Bond equation) B=36 x (F80)1/2 x [(SgxWi)/(100xCsxDe 1/2)]1/3 Where – After work inside the millCalculation quantity of ball charge and filling degreeSample sieve analysisCement Separator Ball Mill OptimizationA Slice Mill is the same diameter as the production mill but shorter in length Request Price Quote Click to request a ball mill quote online or call 6303503012 to speak with an expert at Paul O Abbe® to help you determine which design and size ball mill would be best for your process See our Size Reduction OptionsVariables in Ball Mill Operation Paul O Abbe®
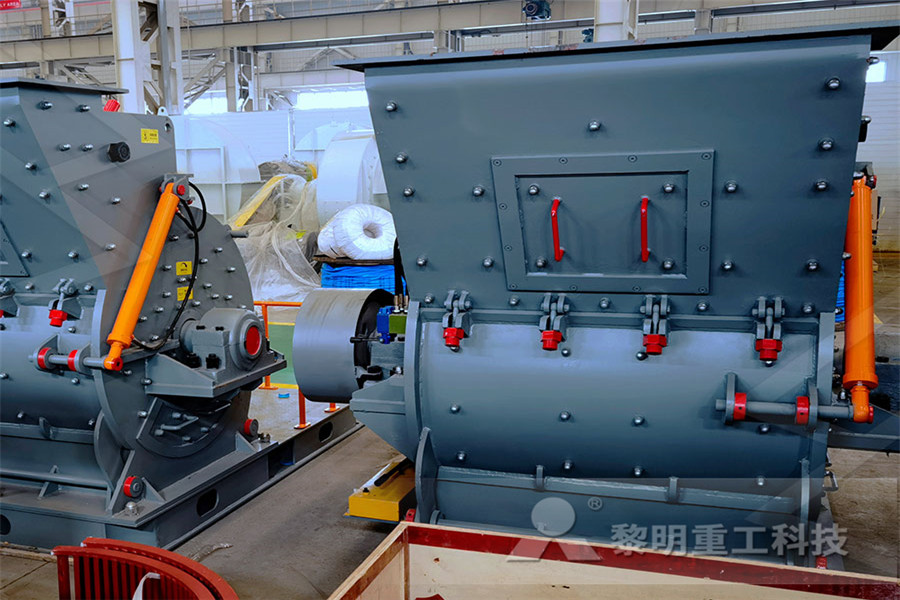
Effect of grinding media properties and stirrer tip speed on
2021年4月1日 Owing to their high energy efficiency, stirred mills are commonly used in the fine or ultrafine grinding of lowgrade and fine disseminated ores to enhance liberation In this study, batch wet grinding studies were conducted in a stirred mill to evaluate the effect of the grinding media density, grinding media diameter, and stirrer tip speed on the 1989年1月1日 INTRODUCTION The energy consumption for grinding, according to Bond (1961), is deter mined by the formula: / 10 10 (I) The work index is determined by grinding experiments carried out in a labo ratory Bond ball mill Based on the results of grinding experiments, numerical values of the work index Wi are calculated according to the Calculation of energy required for grinding in a ball mill2021年10月9日 Once finished the grinding cycles, a minimum of five, the ball mill Bond’s work index w i [kWh/sht] can be calculated using Equation (2) In order to express it in metric tons, the corresponding conversion factor must be used wi = 445 P023 100 gbp082 p 10 P80 p F80 (2) where: w i is the ball mill Bond’s work index [kWh/sht];Variability of the Ball Mill Bond s Standard Test in a Ta 2020年12月4日 E = K (P80 ⁿ – F80 ⁿ ) where K and n are empirical constants measured for your ore One solution for this equation Bond's equation if K = (10Wi) and n = –½ 1 Reference ore Run a P80 of Bond ball mill Work Index tests LinkedIn2020年2月26日 Calculation method and its application for energy consumption of ball mills in ceramic industry based on power feature deployment February 2020 Advances in Applied Ceramics 119(4):112(PDF) Calculation method and its application for energy

Modelling SAG milling power and specific energy
2015年1月1日 The ball charge is a function of the bulk fraction of the SAG mill volume (Jb) occupied by balls; the ore retained in the mill is the result of the volumetric filling which depends on the ore size distribution (specially the % +6″ and the % −6″ +1″), on the rotational speed (N/Nc) and on the solid concentration by weight fraction inside 2009年1月1日 The Bond ball mill work index is an expression of the material’s resistance to ground and a measure of the grinding efficiency The test is a standardized methodology that ends when a circulating load of 250% is obtained In this paper, a new method based on the Population Balance Model (PBM) is proposed and validated to estimate the results Procedure for determination of ball Bond work index in the 2018 Target Operating Hours in Cement industry SNo Department Operating hrs/Day 1 Mines* 10 2 Crusher* 10 3 Raw Mill (Ball mill, VRM) 21 Raw mill (Roller press) 20 4 Coal mill (Ball mill, VRM) 21 5Ball Mill Performance Efficiency Formulas INFINITY FOR CEMENT EQUIPMENT2021年7月18日 The formula for calculating critical mill of speed: N c = 423 / √ (D – d) Where: N c = Critical Speed of Mill D = Mill Diameter d = Diameter of Balls Let’s solve an example; Find the critical speed of mill when the mill diameter is 12 and the diameter of balls is 6 This implies that;How to Calculate and Solve for Critical Mill of Speed Ball Mill Later, many other research efforts were made to define the relationship between S i and J under different operating conditions These studies focused on the determination of S i using the grinding kinetic model More specifically, Deniz V and Onur T (2002) investigated the breakage kinetics of pumice samples in relation to the powder filling volume in a ball mill, Identification of Optimal Mill Operating Parameters during Grinding
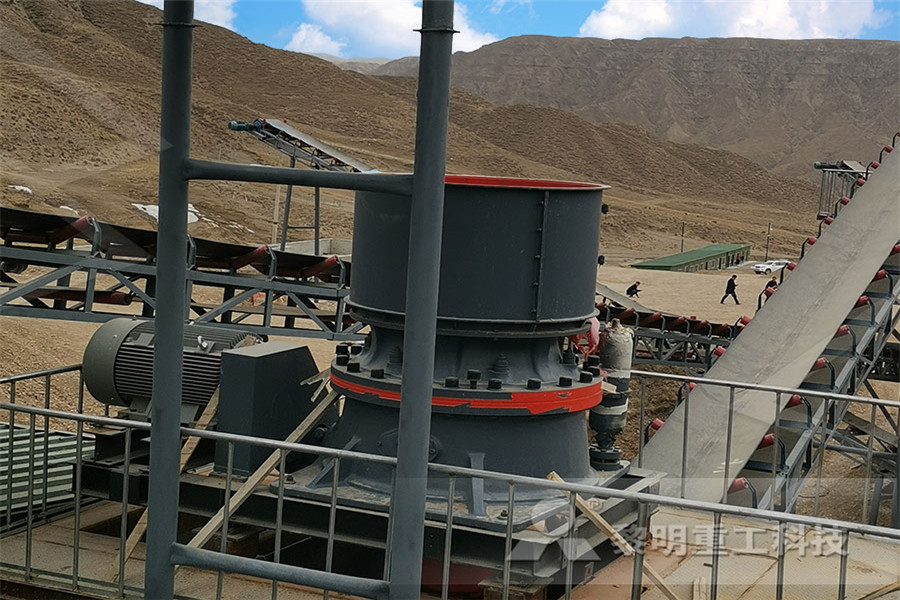
Ball Mill an overview ScienceDirect Topics
where d bmax is the maximum size of feed (mm); σ is compression strength (MPa); E is modulus of elasticity (MPa); ρb is density of material of balls (kg/m 3); D is inner diameter of the mill body (m) Generally, a maximum allowed ball size is situated in the range from D /18 to D/24 The degree of filling the mill with balls also influences productivity of the mill 2020年12月17日 With ballmill grinding being one of the most energyconsuming techniques, setting the optimal values of the operational and mineralogical parameters for efficient grinding is a key target in mineral processing plants [6,7,8,9,10] Ball size is one of the key factors of ballmill efficiency [11,12], and may have a significant financial impact Kinetics of DryBatch Grinding in a LaboratoryScale Ball Mill 2023年10月18日 You need a twostage solution, first stage opencircuit mill and then second stage closedcircuit mill First stage, will be broken into two parts as well, you use a Bond rod mill work index for the coarse component of the ore (+21 mm) and the Bond ball mill work index for the fine component (21 mm)Bond Work Index (Energy equation) Grinding Classification Circuits 2018年12月9日 equation for ball mill circuits • Define and calculate the classification system efficiency of a ball mill circuit • Define and calculate the grinding efficiency of the ball mill in a ball mill circuit • Relate overall ball mill circuit output and circuit efficiency to specific design and operating variablesMODULE #5: FUNCTIONAL PERFOMANCE OF BALL Grinding tests were conducted using a pearshaped ball mill on an oxidized coppercobalt ore to determine the milling parameters Twelve monosized fractions of the ore sample were prepared and Ball mill characteristics and test conditions Mill Diameter, D

Closed circuit ball mill – Basics revisited ScienceDirect
2013年4月1日 Introduction Over the years, ball mill circuits closed with cyclones have become an industry standard, and since the early days, it has been recognised that classification efficiency and circulating load both have a major effect on the efficiency of closed circuit grinding (ie its capacity to produce the desired final product)2015年6月19日 A Ball Mill Critical Speed (actually ball, rod, AG or SAG) is the speed at which the centrifugal forces equal gravitational forces at the mill shell’s inside surface and no balls will fall from its position onto the shell The imagery below helps explain what goes on inside a mill as speed varies Use our online formula The mill speed is typically defined Ball Mill Critical Speed 911 Metallurgist2013年7月15日 In the standard AC closed circuit ball mill grindability test the work index is found from where Pi is the opening in microns of the sieve mesh tested, and Gbp is the net grams of mesh undersize produced per revolution of the 12″ x 12″ test ball mill The closed circuit 80% passing size P averages P1/log 20 for all sizes larger than 150 meshBond Work Index FormulaEquation 911 Metallurgist2002年11月1日 The effect of ball load composition, by varying the grinding media size distribution (eg alternatively by mixing four groups of 195, 38 mm; 195, 50 mm; 38, 50 mm and 195, 38, 50 mm), on the The energy efficiency of ball milling in comminution2020年2月18日 The rotation speed of a mill is an important factor related to its operation and grinding efficiency Analysis and regulation of the optimal speed under different working conditions can effectively reduce energy loss, improve productivity, and extend the service life of the equipment However, the relationship between the optimal speed and different Optimal Speed Control for a SemiAutogenous Mill Based on Discrete