Diagrams Mining Mill In The Cement Factory
2020-02-15T17:02:33+00:00
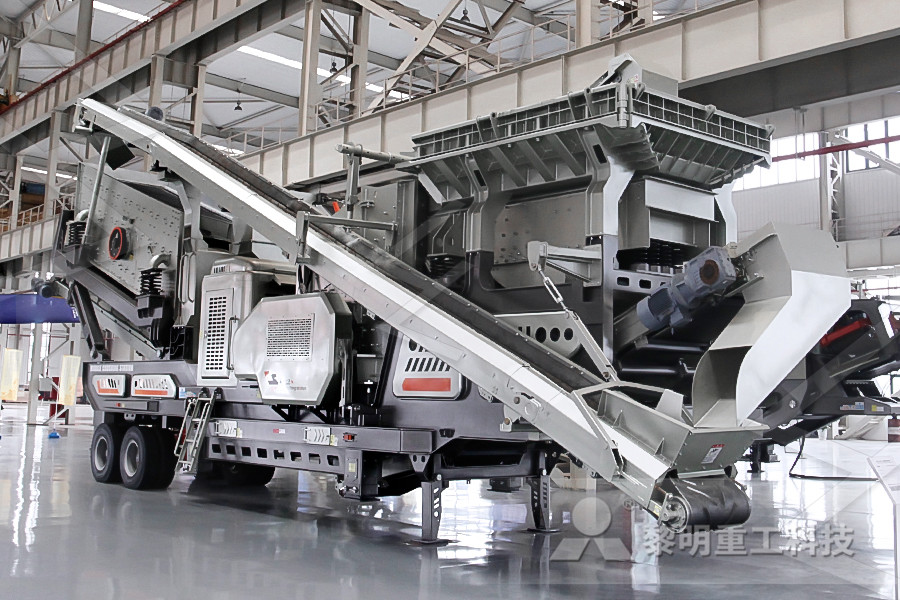
Modeling of energy consumption factors for an industrial cement
2022年5月9日 By initiating a CL for an industrial cement vertical roller mill (VRM), this study conducted a novel strategy to explore relationships between VRM monitored operational 2022年7月4日 There are two open pit mines, namely Livwezi and Chikoa, at Shayona Cement factory in Kasungu They conduct all mining activities including drilling, blasting (PDF) Mining Activities, Cement Production Process and2021年2月16日 the grinding circuit of a raw mill are an increase in output and a reduction in power consumption Expert Optimizer has been successfully applied in more than 90 Industrial : Optimization for the Cement Industry ABB2020年5月1日 In this work, the energy and exergy analyses of a cement ball mill (CBM) were performed and some measurements were carried out in an existing CBM in a Energy and exergy analyses for a cement ball mill of a new PDF On May 13, 2021, Elshan Moradkhani and others published Intelligent Modeling of Cement Plant Mill Unit Using Artificial Neural Networks and Real Data Find, read and (PDF) Intelligent Modeling of Cement Plant Mill Unit Using

Production diagram for cement manufacturing process (A
Download scientific diagram Production diagram for cement manufacturing process (A "2:2" raw to cement mill configuration is shown) from publication: Integrated Power 2012年6月1日 During grinding process, the energy obtained from the rotary burner is consumed In this study, the first and second law analysis of a raw mill is performed and Reducing energy consumption of a raw mill in cement industry2016年1月20日 Thus, the production of cement involves mining; crushing, and grinding of raw materials (principally limestone and clay); calcining the materials in a rotary kiln; Analysis of material flow and consumption in cement160+ million publication pages 23+ billion citations Join for free Download scientific diagram CEMENT MANUFACTURING PROCESS FLOW CHART from publication: Industrial Geology ResearchGate CEMENT MANUFACTURING PROCESS FLOW 2013年1月1日 The ideal clinker is high in silicates and low in free lime which has not combined into the four minerals species found in sound clinker and which can produce Coal utilisation in the cement and concrete industries

Cement Dust an overview ScienceDirect Topics
Cement kiln dust is a fine powdery material generated as a byproduct of Portland cement manufacturing and can be used to create blended concretes ( Kunal Rajor, 2012 ) This solution helps to minimize the amount of material landfilled and the amount of clinker required in cement production2020年7月20日 Step 1: Mining The first step of Cement manufacturing process is to quarry the principal raw materials, mainly limestone, clay, and other materials Step 2: Crushing and slag for slag cement are all Cement manufacturing process: Stepbystep guide2022年7月4日 Figure 28: Showing the raw mill at stationary, Shayona cement factory The raw mill has capac ity of 50 tons per hour and takes 300KW of electricity The mill’s main(PDF) Mining Activities, Cement Production Process and2015年12月9日 Table 1 Raw materials are used to produce the main cement elements (Mohsen, 2015) • Quarry The process of obtaining raw materials for cement manufacturing involves mining and quarrying natural (PDF) Cement Manufacturing ResearchGate2020年11月9日 a lignite mine but one of the most important is a transportation system [1] According to the study reported by Mobley, from 15% to 40% (average 28%) of total production cost is attributed to maintenance activities in the factory [2] The complexity of maintenance in modern mining systems is based on theMaintenance of Bucket Elevator (Case of the Cement

How to Start a Cement Factory
1 Clarify Your Production Scale and Cement Type The first thing to do when you are planning to start a cement factory is to determine which type of cement you are going to produce and how many tons you are going to produce per day The most widely used cement for concrete works is ordinary portland cement (OPC), apart from that, there is 2 天之前 Stage of Cement Manufacture There are six main stages of the cement manufacturing process Stage 1: Raw Material Extraction/Quarry The raw cement ingredients needed for cement production are limestone (calcium), sand and clay (silicon, aluminum, iron), shale, fly ash, mill scale, and bauxite The ore rocks are quarried and How Cement is Made Cement Manufacturing ProcessContribute to chengxinjia/ development by creating an account on GitHub/ layout diagram for cement mill motormd at main2021年5月13日 Intelligent Modeling of Cement Plant Mill Unit Using Artificial Neural Networks and Real Data 101109/SIBCON504192021 Conference: 2021 International Siberian Conference on Control and (PDF) Intelligent Modeling of Cement Plant Mill Unit Using 2018年8月3日 Cement making process Steelmill scale 25 11 899 40 TYPICAL COMPOSITION OF RAW MATERIALS Kiln Process Thermochemical Reactions General Diagram of Preheater Reactions In the tower, Preheaters do 40 80% calcination Precalciners do 70 to 96% calcinationCement Manufacturing Institute for Transportation

Cement Mining Process: A StepbyStep Guide
From cement grinding mills, cement is transported to silos (huge storage tanks), bagged in 20–40 kg amounts Only a tiny portion of the product is packaged for consumers who need small quantities In the Cement 2 天之前 Cement emissions intensity has remained relatively stable since 2018, at just under 06 t CO 2 per tonne of cement produced, following several years of modest increase largely due to an increasing clinkertocement ratio in China To get on track with the NZE Scenario, emissions must fall by an average of 3% annually through to 2030Cement IEA International Energy AgencyContribute to chengxinjia/ development by creating an account on GitHub/ cement mill outlet diagram drawingmd at main2014年4月1日 Faulttree diagrams use logical operators, principally the “OR” and “AND” gates In AND gate the output event occurs if any of the input events occur The factory can be divided to six branches: mine, crushing and mixing bed hall, raw mill, cement mill, burning (clinkerization process), and packing house departments in the first Fault tree analysis of failure cause of crushing plant and Pollutants and pollution control in the cement industry Vipin Kant Singh, in The Science and Technology of Cement and Other Hydraulic Binders, 2023 112 Environmental noise pollution Health organizations are increasingly placing emphasis on the environmental aspects of their activities, products or services 1,2 Noise is defined as an unwanted Cement Plant an overview ScienceDirect Topics
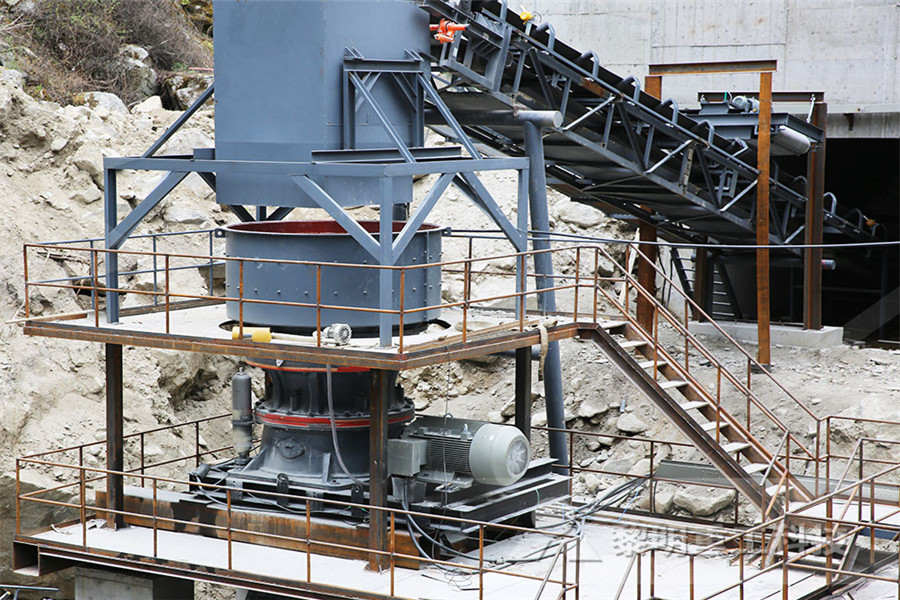
Coal utilisation in the cement and concrete industries
2013年1月1日 Abstract: The utilisation of coal in the cement and concrete industries takes three basic forms: 1 As a fuel in the production of cement clinker, 2 Ash produced by burning coal in power stations is used as a component in cement rotary kiln feeds, 3 Ash produced by burning coal in power stations is used as a mineral additive in concrete mixes2019年7月20日 The quarry (where the mining activity is performed) is located 07 km away from in line 1 and two Roller press+closed circuit ball mill in line 2) based on the type of cement to be produced keeping the quality of cement equal or above the required standard For instance (Clinker+Pozzolana+Gypsum) are proportioned and milled (Process and CEMENT PRODUCTION AND QUALITY CONTROL A 2015年3月1日 There is a more potential in a cement factory for electric power generation using waste heat recovery compared to the other industries A case study has been done at a cement factory having two units, 1600 TPD and 5500 TPD, identified three waste heat rejections at 176 °C, 330 °C and 420 °C and designed a suitable power plant Design and analysis of a cogeneration plant using heat The purpose of the primary crusher is to reduce the ROM ore to a size amenable for feeding the secondary crusher or the SAG mill grinding circuit The ratio of reduction through a primary crusher can be up to about 8:1 Feed: ROM up to 15 m Product: 300mm (for transport) to 200mm (for SAG mill) Feed Rate:AMIT 135: Lesson 5 Crushing – Mining Mill Operator Training2023年10月19日 Step 1: Mining The cement manufacturing process starts from the mining of raw materials that are used in cement manufacturing, mainly limestone and clays A limestone quarry is inside the plant area and a clays quarry is as far from the plant area as 25 km The limestone is excavated from open cast mines after drilling and blasting and Manufacturing process Lafarge

Mathematics Free FullText An Optimized Open Pit Mine
2022年11月6日 This study involves a working limestone mine that supplies limestone to the cement factory The two main goals of this paper are to (a) determine how long an operating mine can continue to provide the cement plant with the quality and quantity of materials it needs, and (b) explore the viability of combining some limestone from a nearby mine with 2022年1月1日 Concrete is the most commonly used of all the building materials in the world due to its unique advantages compared to other materials [1]The main reasons for its fame are because concrete has excellent mechanical feature and affordable [2], [3], [4], [5]It also has the tendency to be designed into a variety of sizes and forms [6]Moreover, the Environmental impact of cement production and Solutions: 2016年1月20日 The results show that approximately 248 t, 469 t, and 341 t of materials are required to produce a ton of the product in raw material preparation, clinker production, and cement grinding stages, and their waste rates are 6331%, 7412%, and 7889%, respectively The recycling rate of wastes during clinker production is remarkably higher Analysis of material flow and consumption in cement2020年8月25日 There are three steps of the hightemperature system: Drying or preheating, calcining, and sintering The calcining is the core part of the clinker production; the raw meal is weighed and sent into preheater and cement kiln to process clinker Grate cooler helps to cooler clinker, the cooled clinker is sent to the cement silo for storageCement Production Process AGICO2022年10月11日 The raw cement ingredients are heated and clinkers or hard, spherical nodules are produced as a result Cement Kiln processing involves the following stages: drying or preheating, calcining, and clinker cooling Calcination is the process of burning the raw mix at a high temperature so that clinkers are formedThe Cement Manufacturing Process Environmental and Social

Jaypee Group Businesses CementManufacturing Process
2023年6月21日 The cement manufacturing process starts from the mining of limestone, which is the main raw material for making cement (for PPC) are extracted from their respective hoppers and fed to the Cement Mills These Ball Mills grind the feed to a fine powder and the Mill discharge is fed to an elevator, which takes the material to a 2016年2月24日 stock and provide spare parts close to the mining operation Good geotechnical information is essential to crushing plant siting and design Installing a primary crushing plant on solid rock reduces the cost of concrete and structural steel Life of Mine/Expansion Plans The life of the mine is a key element in the design of any crushing Crushing Plant Design and Layout Considerations 911 Apr 2016 Adem Atmaca Nihat Atmaca In cement industry about 110 kWh of electrical energy is consumed to produce one ton of cement and about 26% of the total electrical power is used during Figure 1 The use of electrical energy in cement production2019年7月30日 Coal is still used in approximately 90% of cement plants globally, to deliver the energy needed for the heat inside the kiln PGNAA analyzers control coal blends to allow cement producers to mix low cost coals with higher costs coals to provide additional cost savings in fuel, and to allow a consistent feed to the kiln Belt scales and tramp 6 Points in the Production Process to Optimize Cement Making2021年2月16日 the mill and the balance of material flows through the system, it is possible to identify situations when the feed to the mill and the output can be increased Increased output over extended periods of time has been observed on mills controlled by Expert Optimizer • Reduced power consumption This important saving is a result of the softerIndustrial : Optimization for the Cement Industry ABB

Cement Manufacturing Process Phases Flow
2012年8月30日 Cement Manufacturing Process Phase 1: Raw Material Extraction Cement uses raw materials that cover calcium, silicon, iron and aluminum Such raw materials are limestone, clay and sand Limestone 4) As the materials pass through the kiln their temperature is rised upto 13001600 °C The process of heating is named as “burning” The output is known as “clinker” which is 0155 cm in diameter 5) Clinker is cooled stored 6) Clinker is ground with gypsum (36%) to adjust setting time(PDF) THE CEMENT MANUFACTURING PROCESSmill Watch 1 Star 0 Fork You've already forked mill 0 Code Issues Pull Requests Packages Projects Releases Wiki Activity You can not select more than 25 topics Topics must start with a letter or number, can include dashes ('') and can be mill / mill/ layout diagram of cement industrymd at master mill 2020年1月1日 The failure modes are determined on the three main machines of cement production process consist of raw mill, kiln, and cement mill The results indicated the highest failure mode in the cement (PDF) Potential Failure Modes of Cement Production2021年5月3日 Energy cost contributes to about 40–50% of cement production cost in Nigeria depending on the production process and type of cement with 1 tonne of cement requiring 60–130 kg of fuel or its equivalent and about 105 kWh of electricity [ 3 ] Fossil fuels like coal, pet coke, fuel oil, and gas are the primary fuels used in the cement kilnsEnergy and Economic Comparison of Different Fuels in Cement

Cement Production an overview ScienceDirect Topics
Assessing the environmental impact of conventional and ‘green’ cement production G Habert, in Ecoefficient Construction and Building Materials, 2014 101 Introduction Cement production has undergone tremendous developments since its beginnings some 2,000 years ago While the use of cement in concrete has a very long history (Malinowsky, 1991), the schematic diagram of comminuting mill gold ore ball mill diagram schematic diagram of crusher plant xsm is a mine mill ball mill diagram in cement find complete details about mine Get a Price Ball Mill Schematic Diagram Mining Ore Processing Newmont Waihi Gold Grinding Flow Diagram The ball mill is very similar to the SAG mill except it has a larger schematic diagram of the cement millCement mill Wikipedia 18 A cement mill (or finish mill in North American usage) is the equipment used to grind the hard,nodular clinker from the Function Of Fls Mining Mill At Mines In Cement Plant A plant or a piece testWhether you are looking for anRoller Mill For Cement FactoryRoller Mill For Cement Factory Production capacity : 0615t h en/cement factory coal mill system testmd at main lbsid/enContribute to changjiangsx/ development by creating an account on GitHub/ plant layout diagrams for miningmd at mainCement kiln dust is a fine powdery material generated as a byproduct of Portland cement manufacturing and can be used to create blended concretes ( Kunal Rajor, 2012 ) This solution helps to minimize the amount of material landfilled and the amount of clinker required in cement productionCement Dust an overview ScienceDirect Topics

Cement manufacturing process: Stepbystep guide
2020年7月20日 Step 1: Mining The first step of Cement manufacturing process is to quarry the principal raw materials, mainly limestone, clay, and other materials Step 2: Crushing and slag for slag cement are all 2022年7月4日 Figure 28: Showing the raw mill at stationary, Shayona cement factory The raw mill has capac ity of 50 tons per hour and takes 300KW of electricity The mill’s main(PDF) Mining Activities, Cement Production Process and2015年12月9日 Table 1 Raw materials are used to produce the main cement elements (Mohsen, 2015) • Quarry The process of obtaining raw materials for cement manufacturing involves mining and quarrying natural (PDF) Cement Manufacturing ResearchGate2020年11月9日 a lignite mine but one of the most important is a transportation system [1] According to the study reported by Mobley, from 15% to 40% (average 28%) of total production cost is attributed to maintenance activities in the factory [2] The complexity of maintenance in modern mining systems is based on theMaintenance of Bucket Elevator (Case of the Cement 1 Clarify Your Production Scale and Cement Type The first thing to do when you are planning to start a cement factory is to determine which type of cement you are going to produce and how many tons you are going to produce per day The most widely used cement for concrete works is ordinary portland cement (OPC), apart from that, there is How to Start a Cement Factory

How Cement is Made Cement Manufacturing Process
2 天之前 Stage of Cement Manufacture There are six main stages of the cement manufacturing process Stage 1: Raw Material Extraction/Quarry The raw cement ingredients needed for cement production are limestone (calcium), sand and clay (silicon, aluminum, iron), shale, fly ash, mill scale, and bauxite The ore rocks are quarried and Contribute to chengxinjia/ development by creating an account on GitHub/ layout diagram for cement mill motormd at main2021年5月13日 Intelligent Modeling of Cement Plant Mill Unit Using Artificial Neural Networks and Real Data 101109/SIBCON504192021 Conference: 2021 International Siberian Conference on Control and (PDF) Intelligent Modeling of Cement Plant Mill Unit Using 2018年8月3日 Cement making process Steelmill scale 25 11 899 40 TYPICAL COMPOSITION OF RAW MATERIALS Kiln Process Thermochemical Reactions General Diagram of Preheater Reactions In the tower, Preheaters do 40 80% calcination Precalciners do 70 to 96% calcinationCement Manufacturing Institute for Transportation